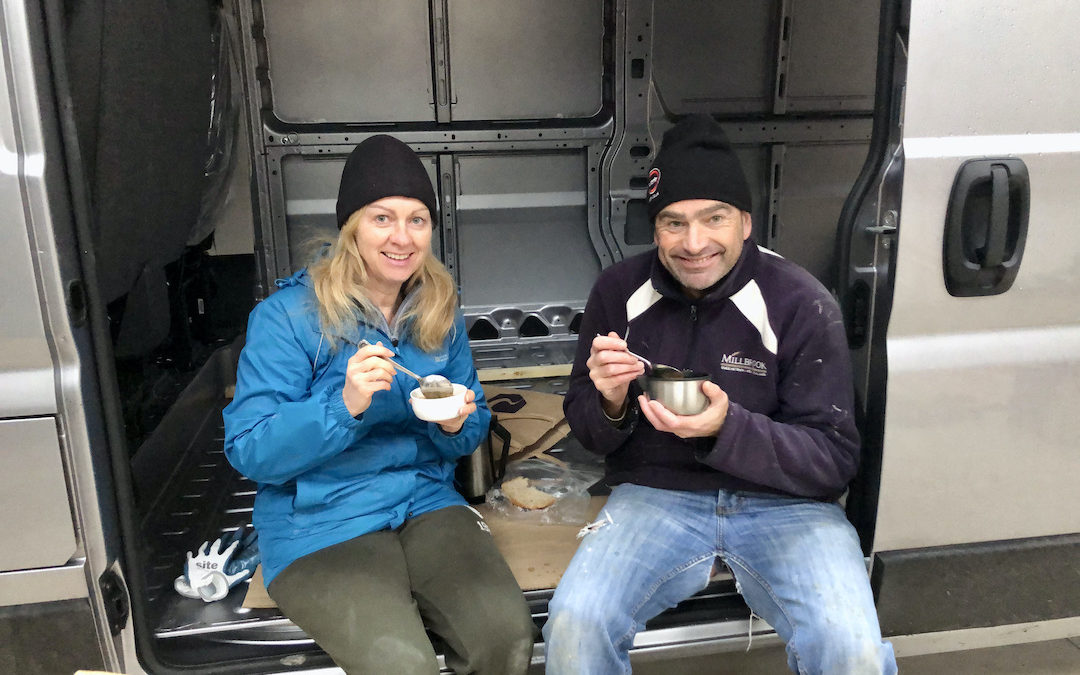
A Step by Step guide to how we built our Citroen Relay camper van
First up we had no experience and no idea where to start on how to build a camper van! That’s where YouTube came in handy. We spent hours sifting through hundreds of YouTube videos on how to build a camper van. Some of it was relevant to us and our van, but so much of it wasn’t. Our logic told us to start from the floor up. After all you’d never start building a home without putting some foundations in first!
Secondly we had no garage to work in! That’s where friends come in handy. A friend very kindly gave us the use of his brand new shed to work in. It was less of a shed, and more of a barn the size of a 5-a-side football pitch! We had oodles of space to spread out, and we could work on the build whatever the weather. And we can tell you it was cold! We take our hats off to anyone who managed to build a camper van in their driveway or on the street, especially if, like us, they built it during the winter.
Armed with the internet and a roof over our heads we started our camper van build the first week of December 2020. Here follows the very rough step-by-step process we used to convert a Citroen Relay panel van into a camper van. There is no guarantee that the same process would work for you, but it might give you a starting point.
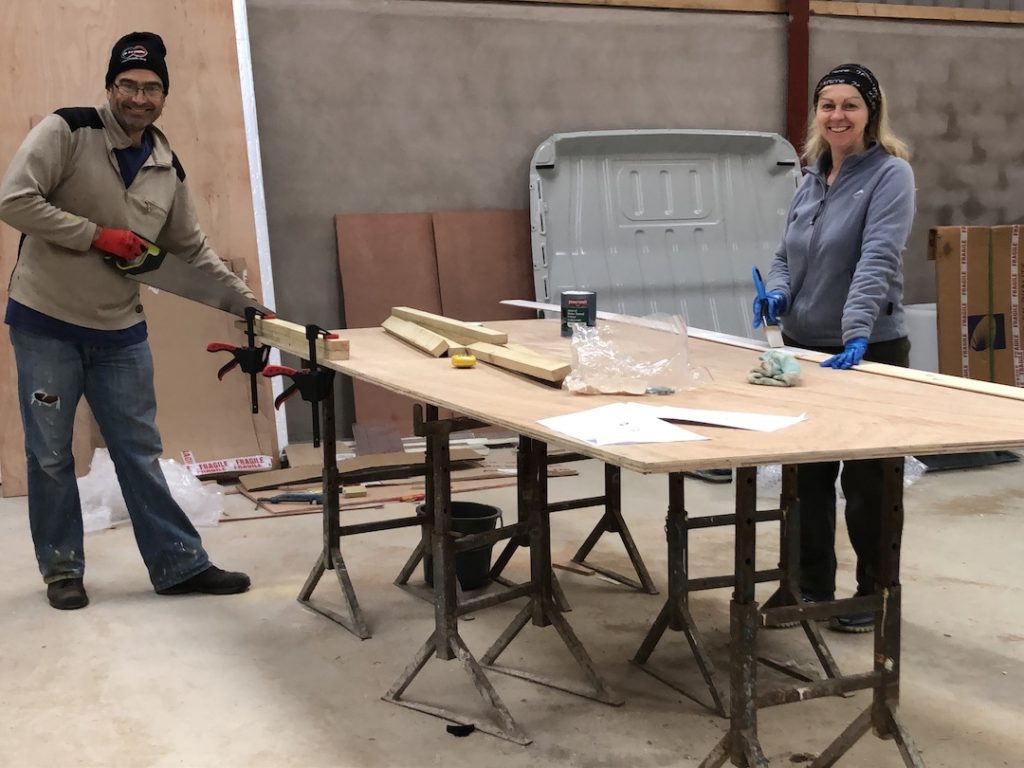
It’s worth saying here that we did have at least a vague design of the layout we wanted before we started the build! We’d gone as far as creating a mock layout of the main features using cardboard boxes to get a feel for how it would all fit. Keep in mind our Citroen Relay van was brand new so we didn’t have to degrease it or treat any rust spots in preparation for the build.
If you want to know why we chose a Citroen Relay van for our camper van build then head over to this blog post.
This post may contain affiliate links. As an Amazon Associate we earn from qualifying purchases. More info in our Privacy Policy.
Our step by step guide to building our campervan
- Removing the bulkhead
- Laying the floor
- Sound deadening
- Installing the roof fan, sky light and windows
- Fitting the solar panel
- Adding a swivel base to the passenger seat
- Ceiling battens & insulation
- Installing a reversing camera & dash monitor
- Electrical System – first fix
- Rear doors
- Walls
- Wheel Arches
- Bathroom window
- Garage
- Ceiling cladding
- Lighting
- Painting
- Electrical System – wiring
- Plumbing & Heating
- Bathroom
- Bedroom
- Kitchen
- Gas installation
- Storage and seating
- Finishing Touches
- Completion!
Removing the bulkhead
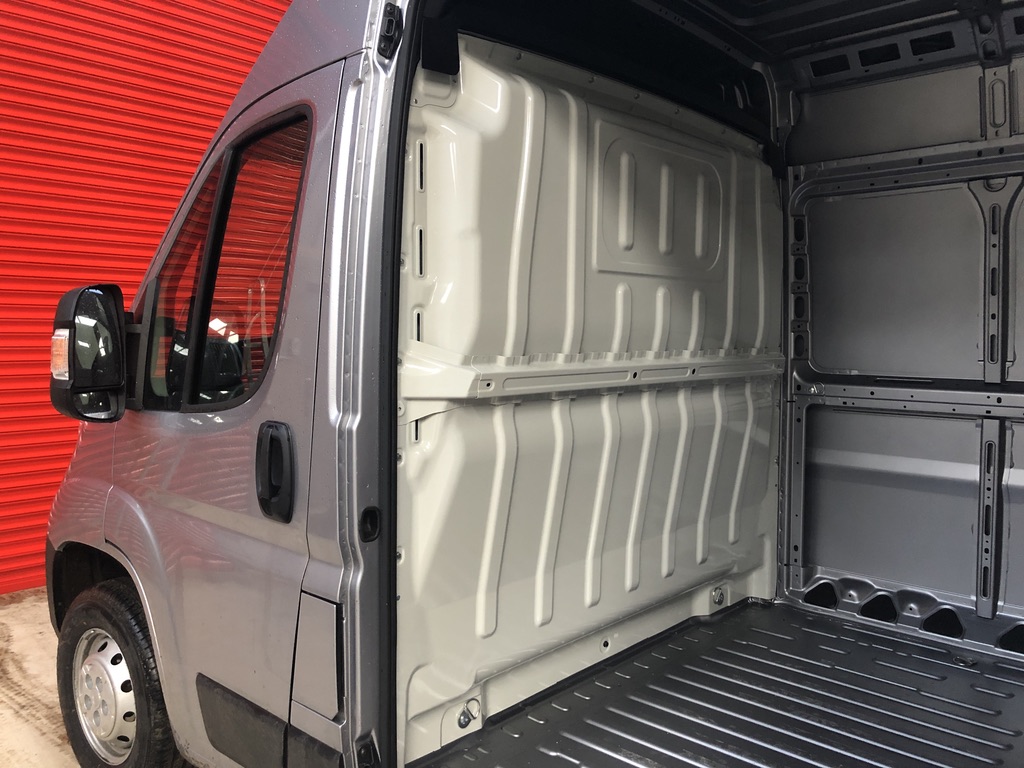
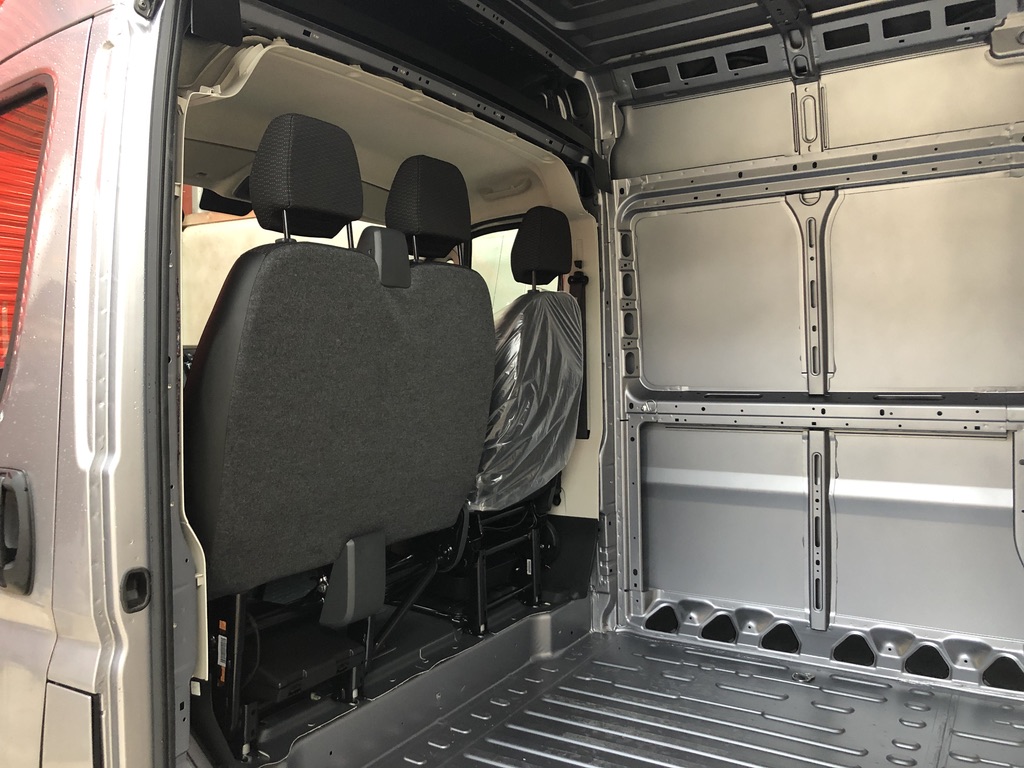
The first thing we did was we removed the bulkhead – the divider between the cab and the rear of the van. In our van design we wanted the area between the cab and the rest of the van to be open so that eventually we could have a walk-through area. This would mean on a rainy day (of which there are many in the UK) we could walk from the cab into the back of the van without having to open the side doors.
It also means you have quick access to the cab should you need to drive away from a park up in the case of an emergency, particularly at night time. Plus it gives you more space to work in during the build process!
Laying the floor
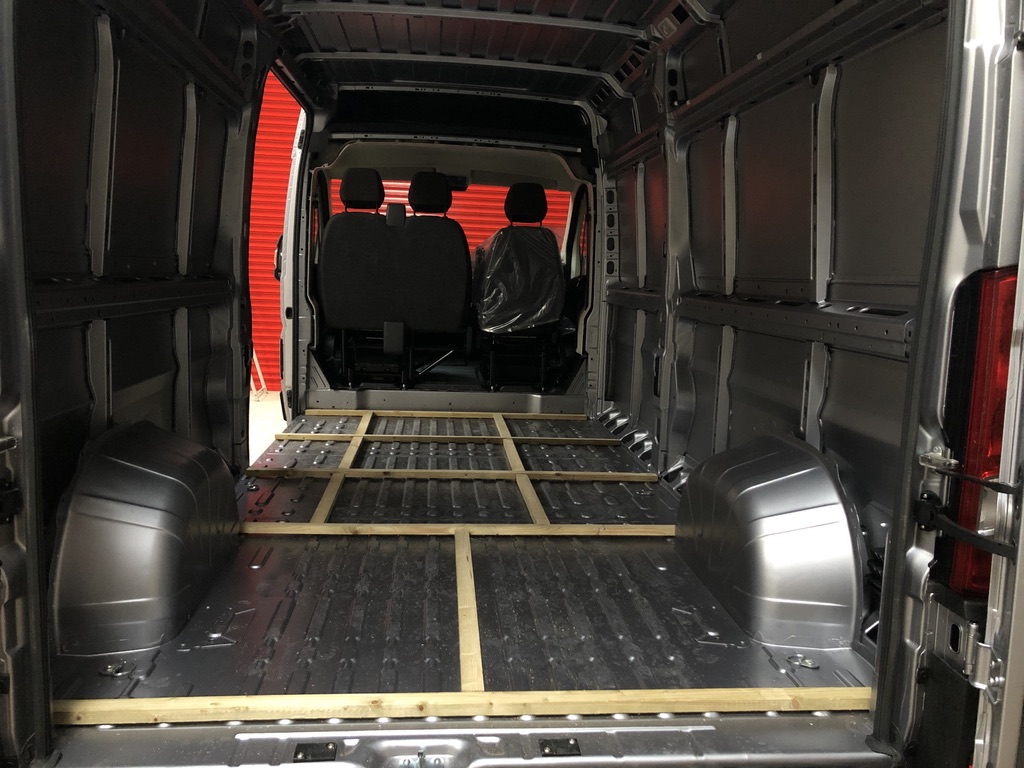
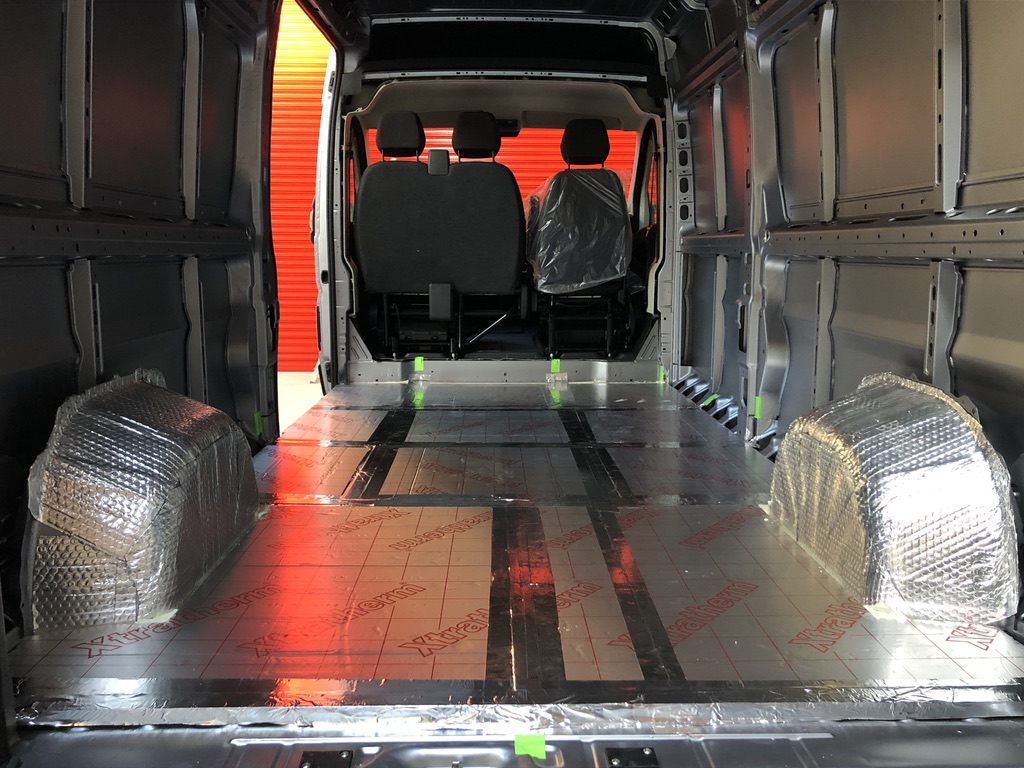
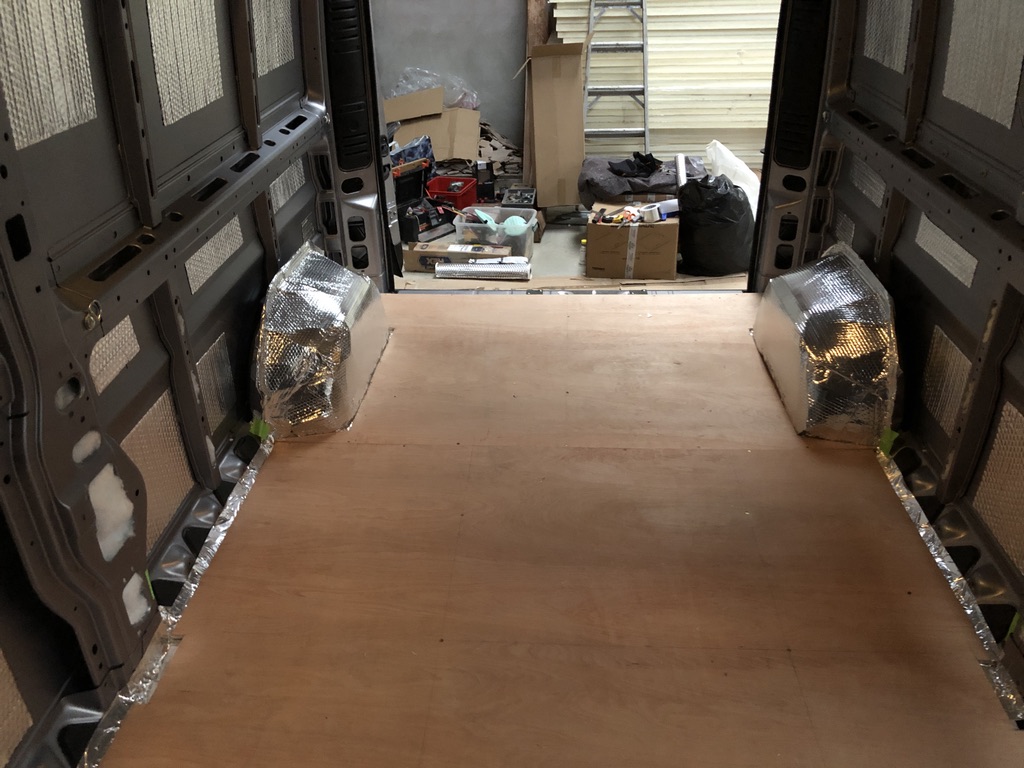
Next up for us was laying the plywood floor – having a level and insulated floor to work on rather than the cold metal corrugated van floor made sense to us. Plus it made it much easier to stand on in winter!
We laid a grid of 2×1 battens using Sikaflex 552 adhesive to fix them to the floor (we didn’t want to drill any unnecessary holes in the floor). We filled the floor grid with rigid insulation boards (25mm thick) and sealed them with aluminium foil tape to create a vapour barrier before we screwed the 12mm ply boards to the battens.
The top floor covering we left to near the end of the build process for two reasons – 1. it would likely get damaged while we work on the van build, and 2. it didn’t make logical or economical sense to us to lay a top floor covering the entire length of the van when at the end of the build you would only see a tiny portion of it.
Sound deadening
A tin van is always going to sound tinny, but adding sound deadening mats to the walls can help to reduce some of the noise, and provide a little extra insulation. We opted for Dodo Mat Sound Deadening and applied it to the wall panels, the overhead cab, the ceiling and the wheel arches. A relatively cheap and easy job to do, made easier by investing in a long reach mini paint roller to smooth out the mats and get rid of any air bubbles.
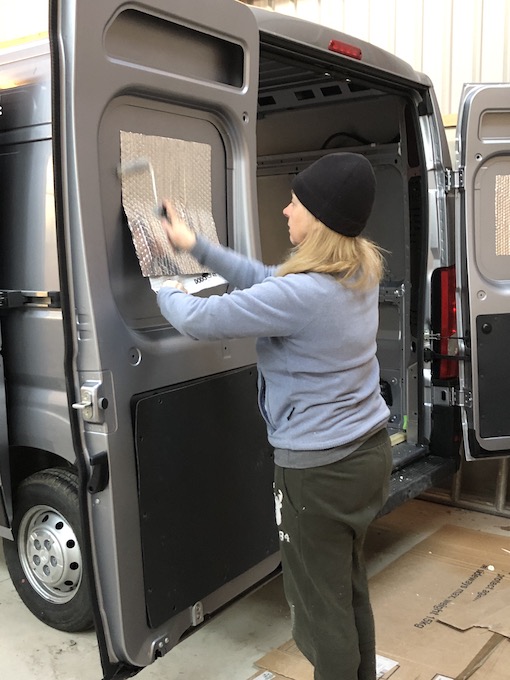
Installing the roof fan, sky light and windows
These jobs were scary! Cutting that first hole in the van is a tense moment to say the least. Make sure you measure at least twice as you can only cut once! We must’ve measured and re-measured a hundred times!
Remember as you cut into the metal, the jigsaw creates loads of tiny metal shards and it is best to clean these up as soon as possible before they create potential rust hazards.
We chose the Maxxair Roof Fan Deluxe 400x400mm with remote control, and the same size Maxxair SkyMaxx sky light with built in blind and flyscreen.
We wanted opening windows rather than glass panels, and shopped around until we found the Polyvision Aero windows we liked. They weren’t cheap, but are double glazed, tinted, and come complete with mosquito nets and blinds. We fitted one window (900x450mm) in the sliding door, and the other window (700x350mm) in the opposite wall.
To seal the fan, roof light and windows we used Sikaflex 552 waterproof sealant which comes in either white, black or grey.
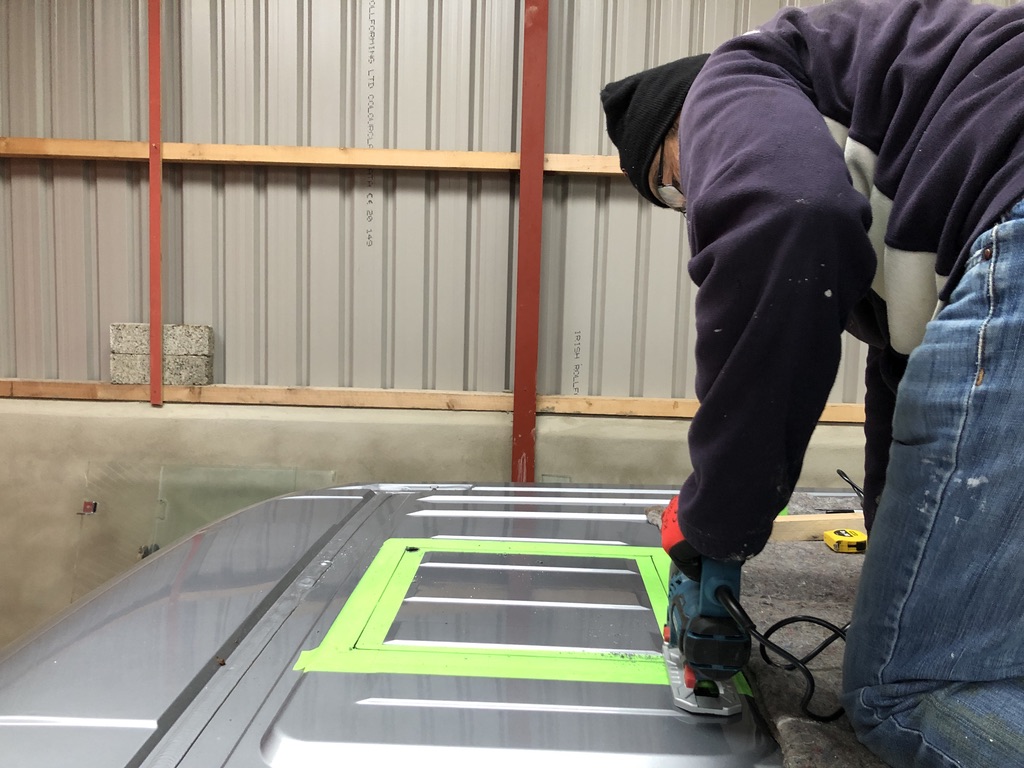
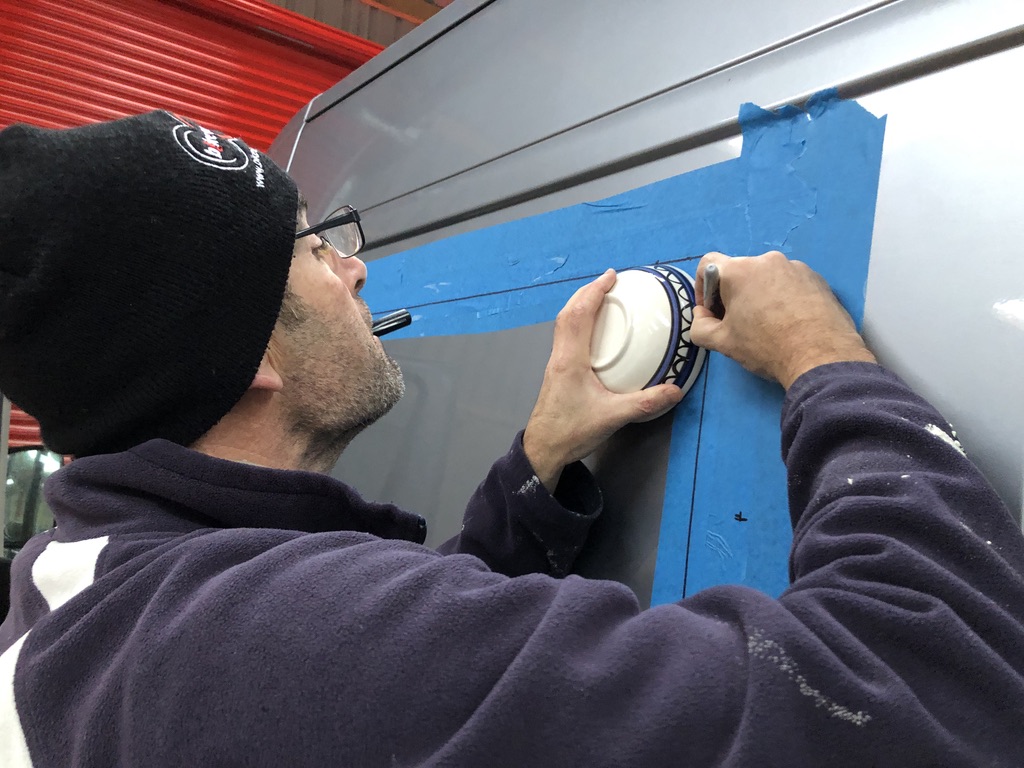
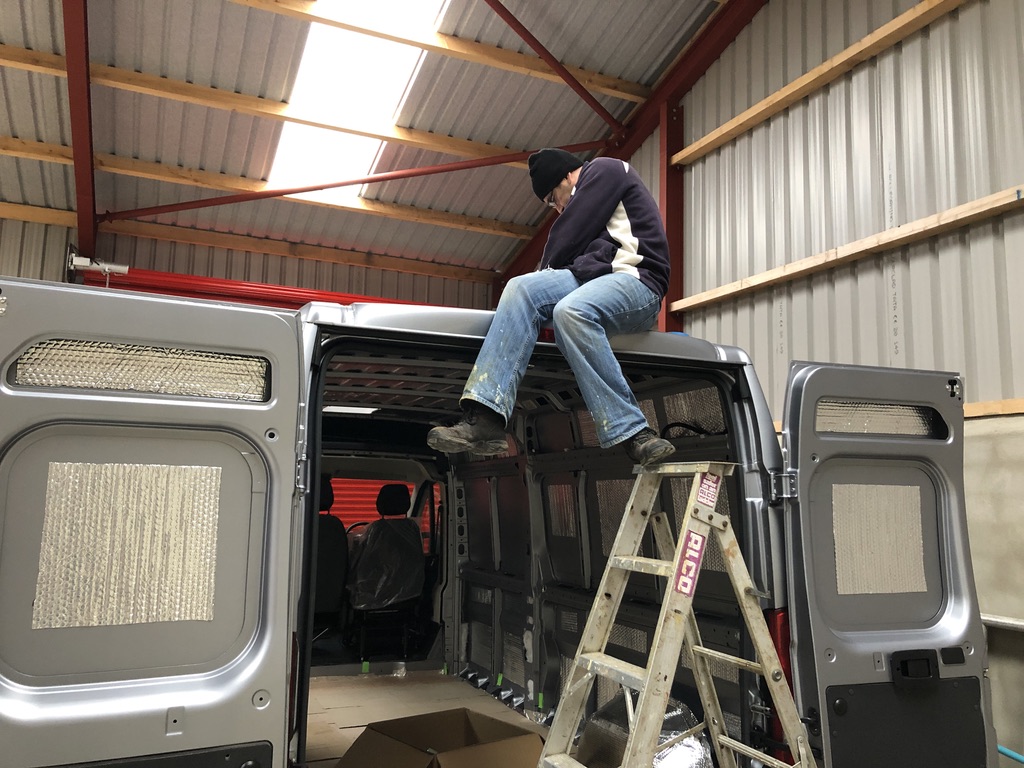
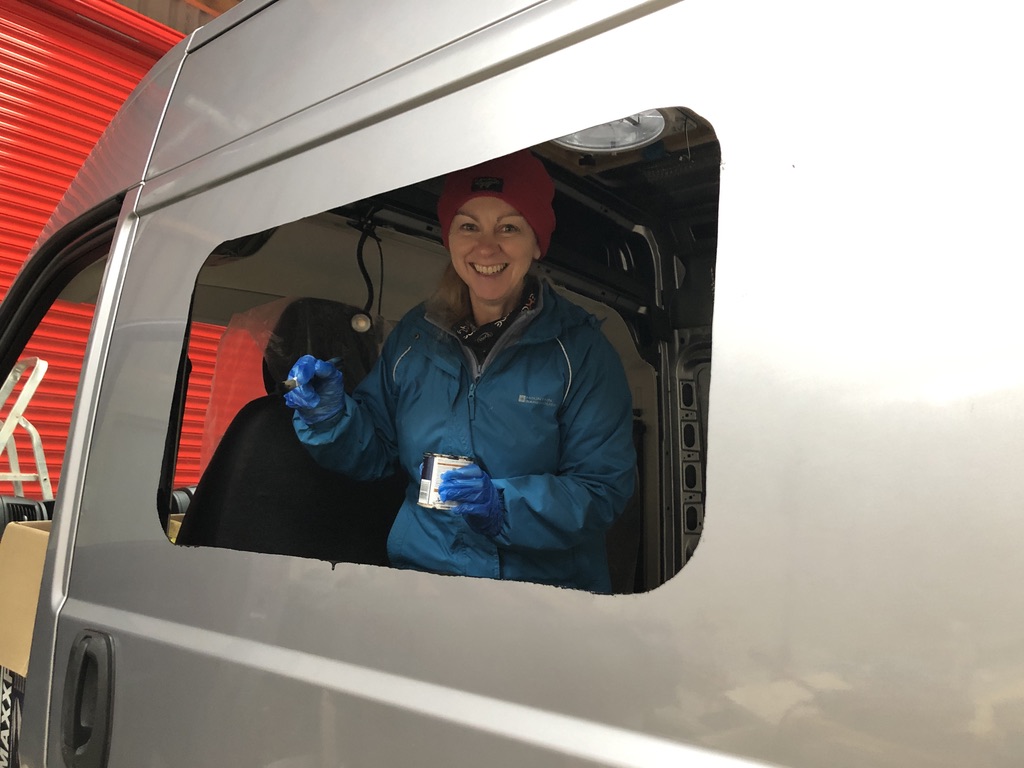
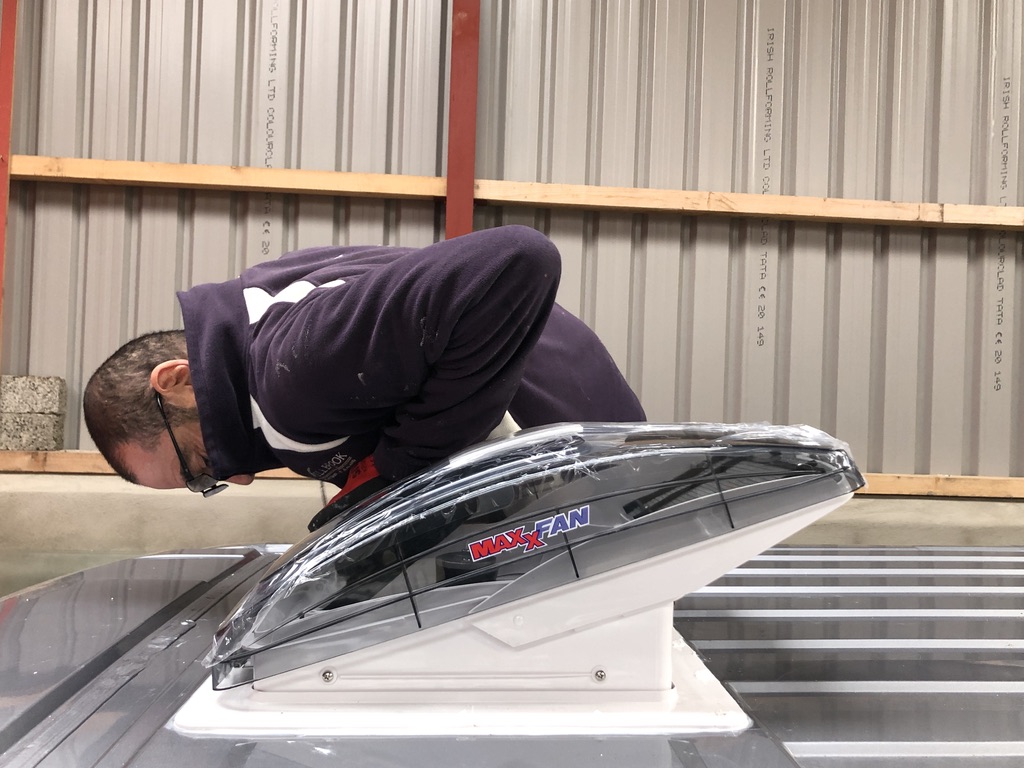
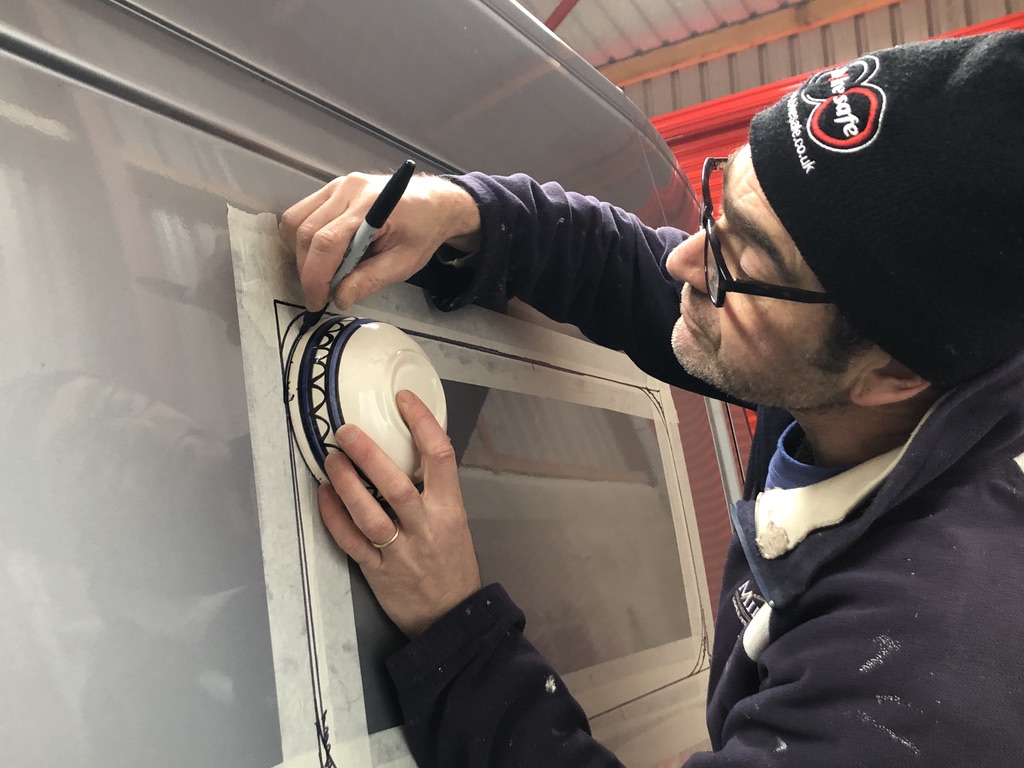
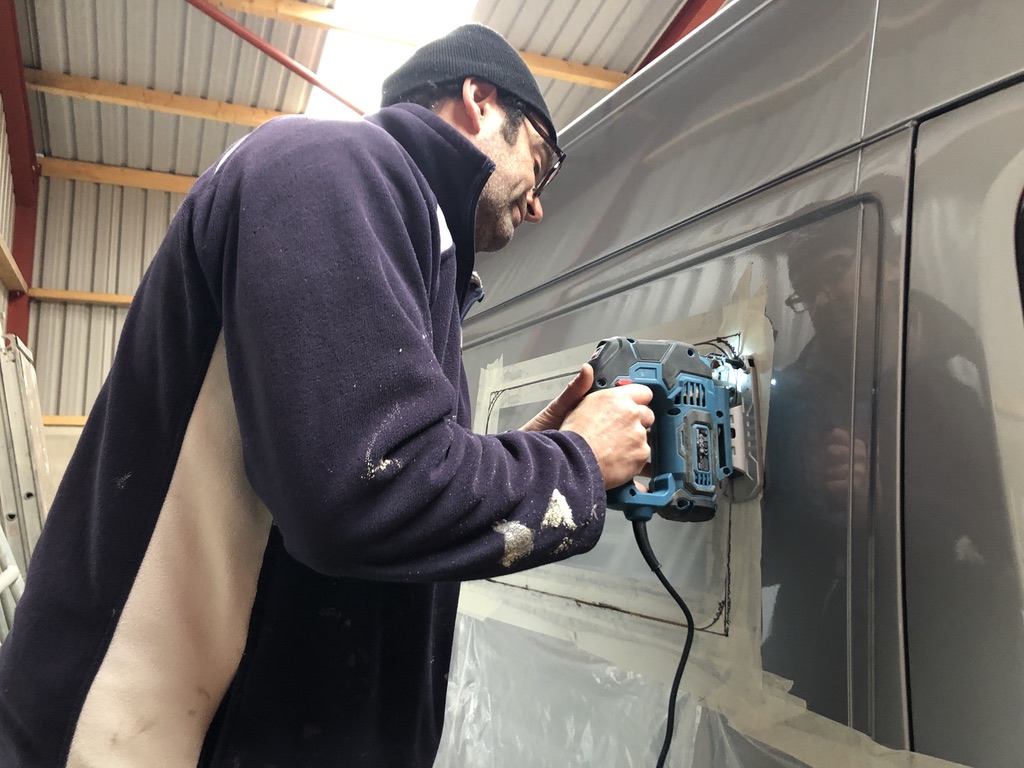
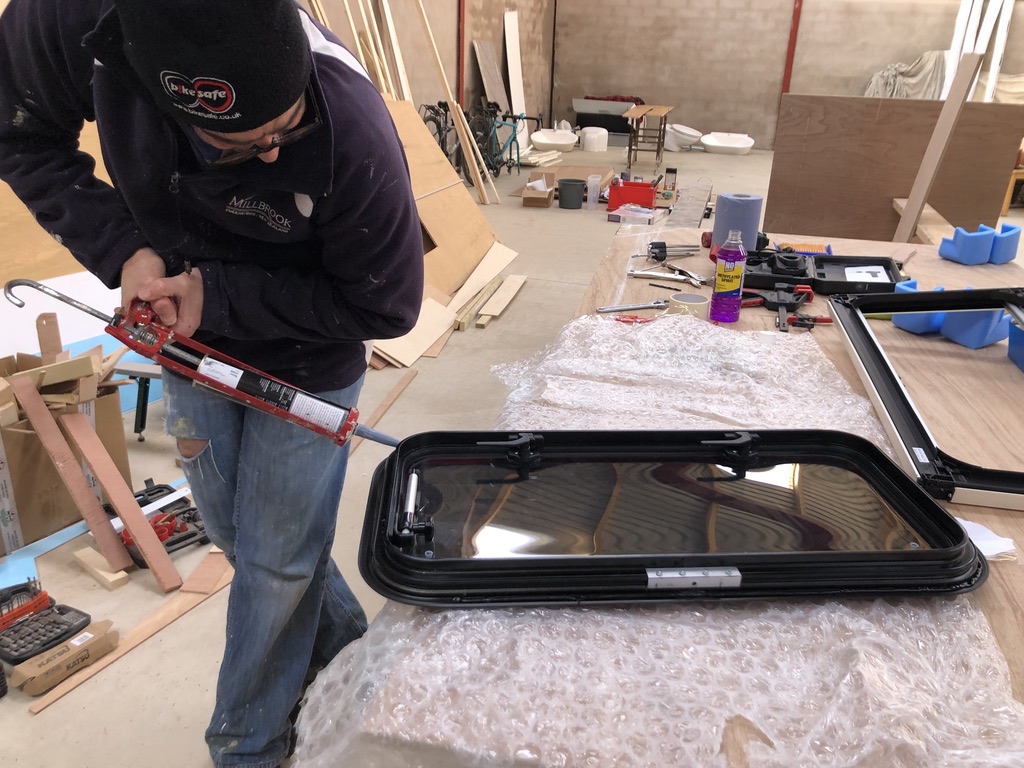
Fitting the solar panel
This was definitely a job for the two of us! We bolted the solar panel to aluminium quadrant brackets and then used the same Sikaflex 552 waterproof sealant to attach it to the roof. The panel we fitted was a Longi 370W split cell solar panel from Plug In Solar.
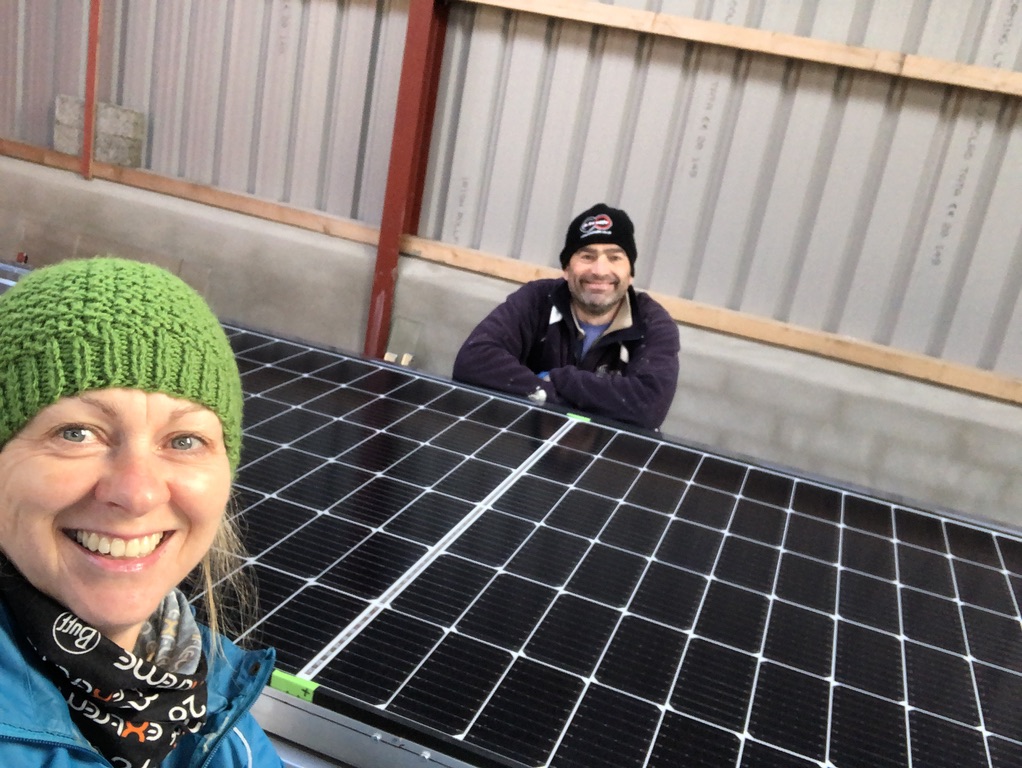
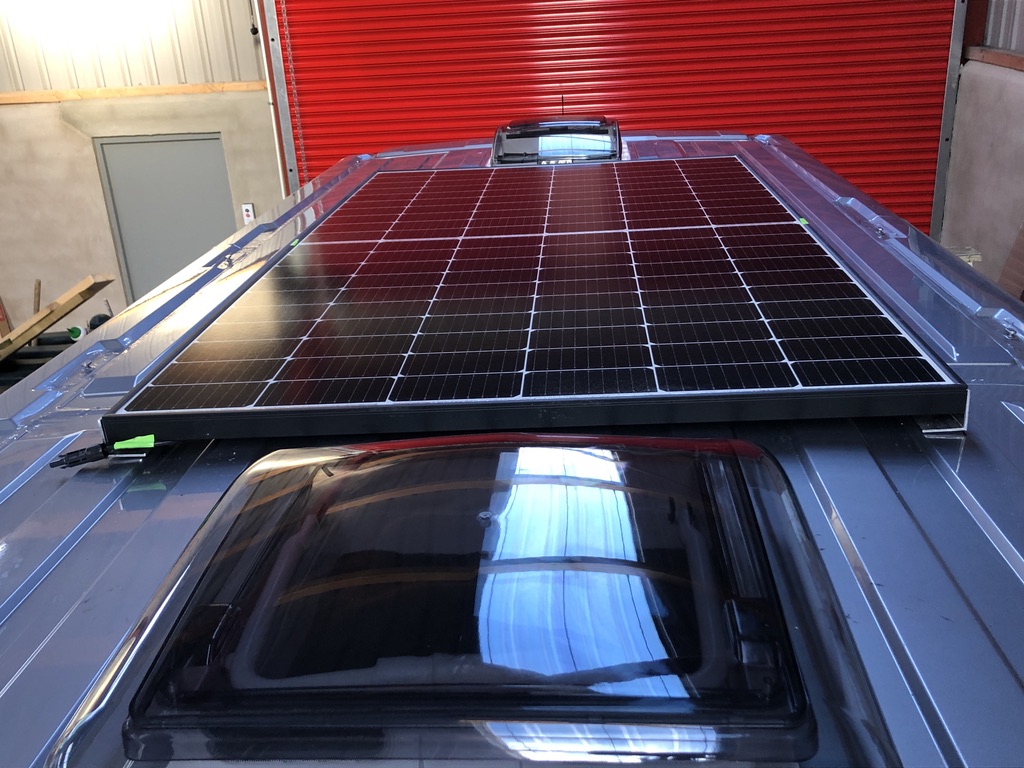
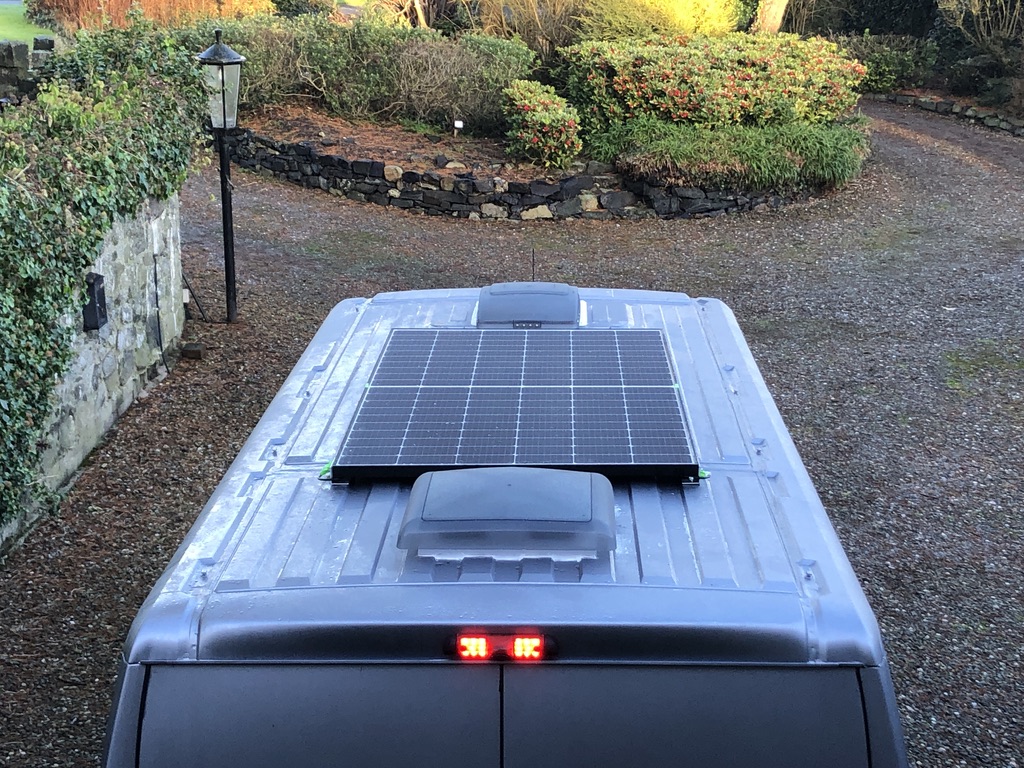
Adding a swivel base to the passenger seat
Our Citroen Relay van came with a fixed double passenger seat, or bench seat as they’re sometimes called. Ideally we wanted to replace it with a single swivel seat, but finding one at a reasonable price during the lockdown of 2020 was proving impossible. Instead we opted for a swivel base for the double seat from Custom Shop Designs.
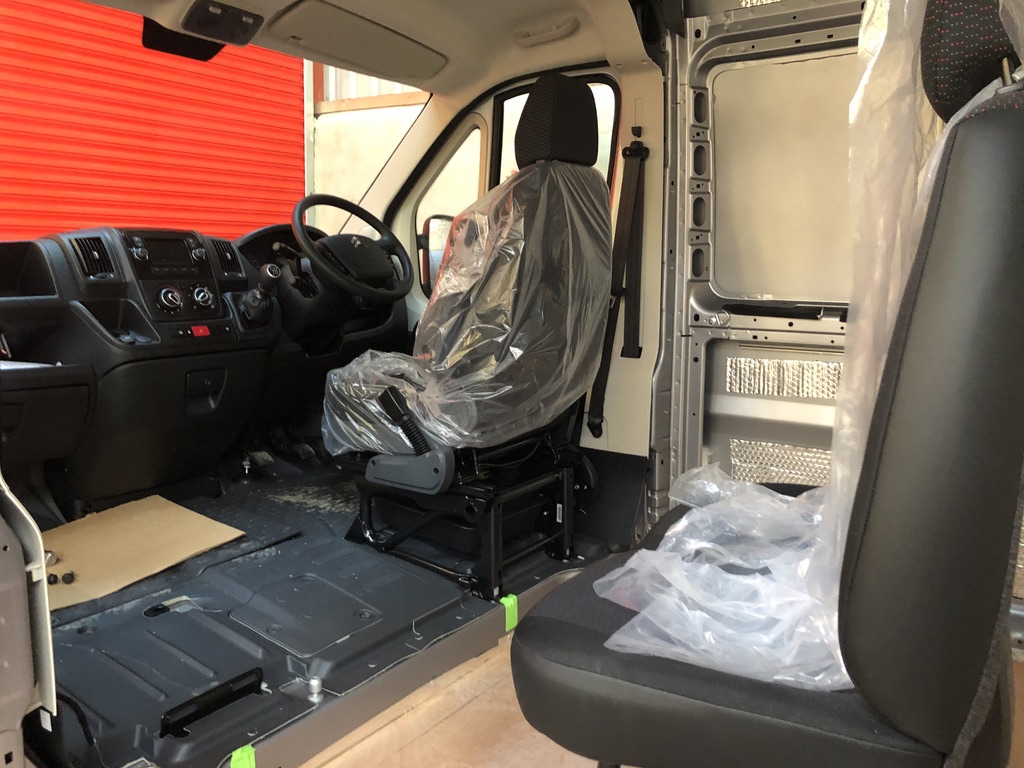
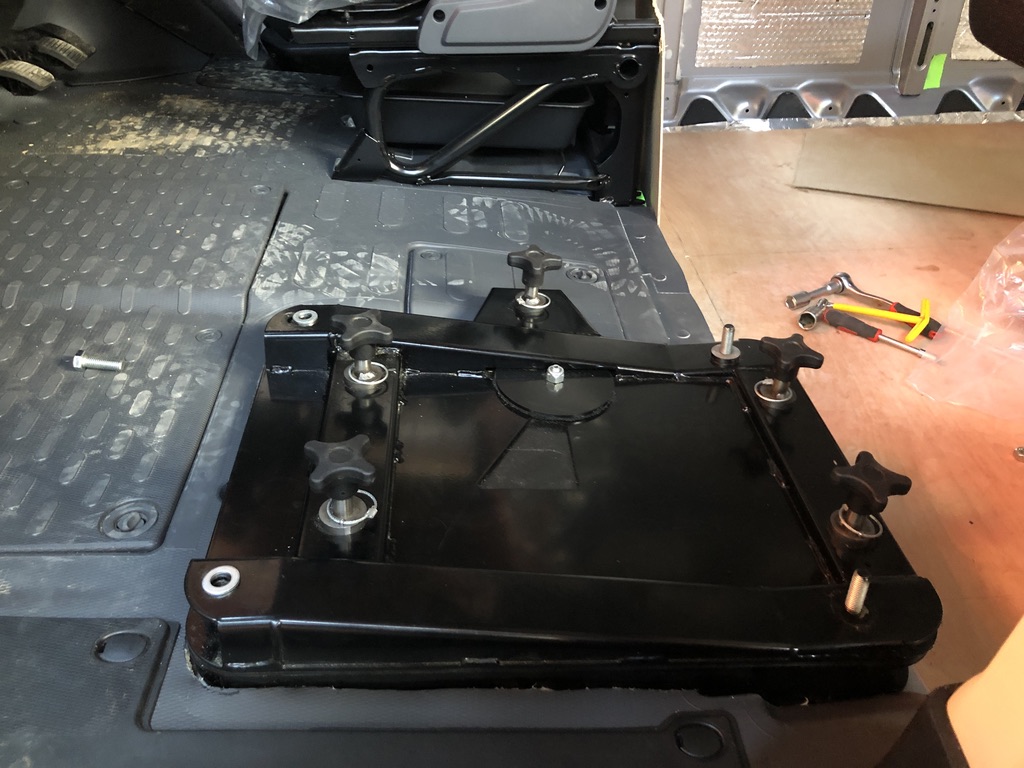
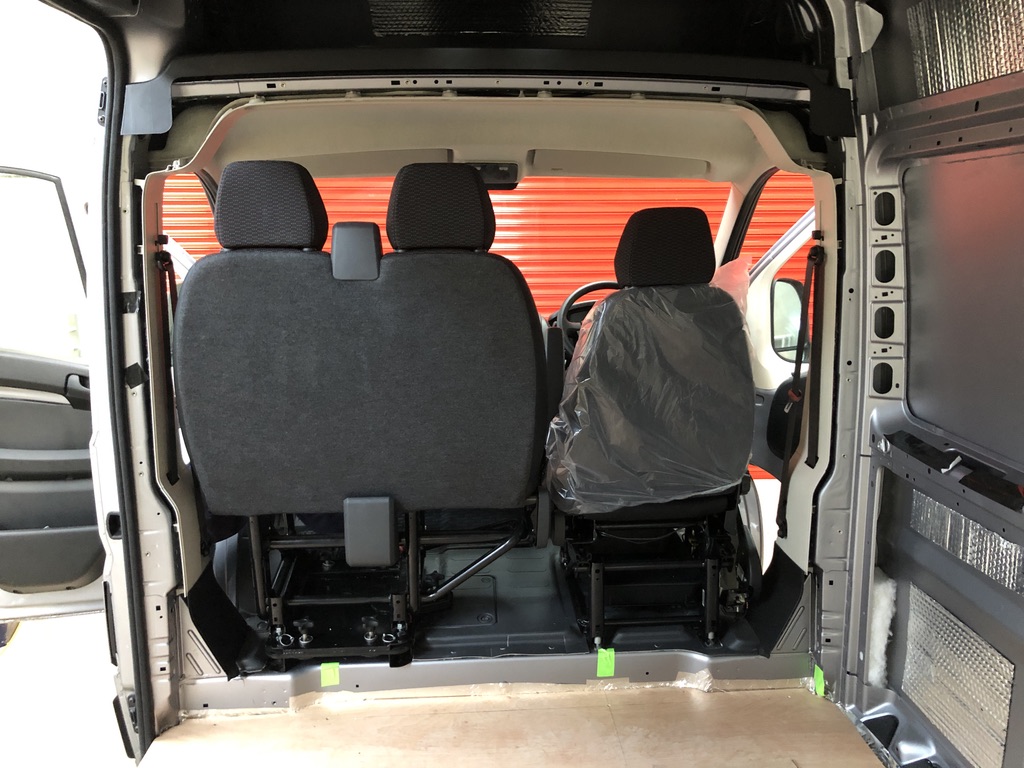
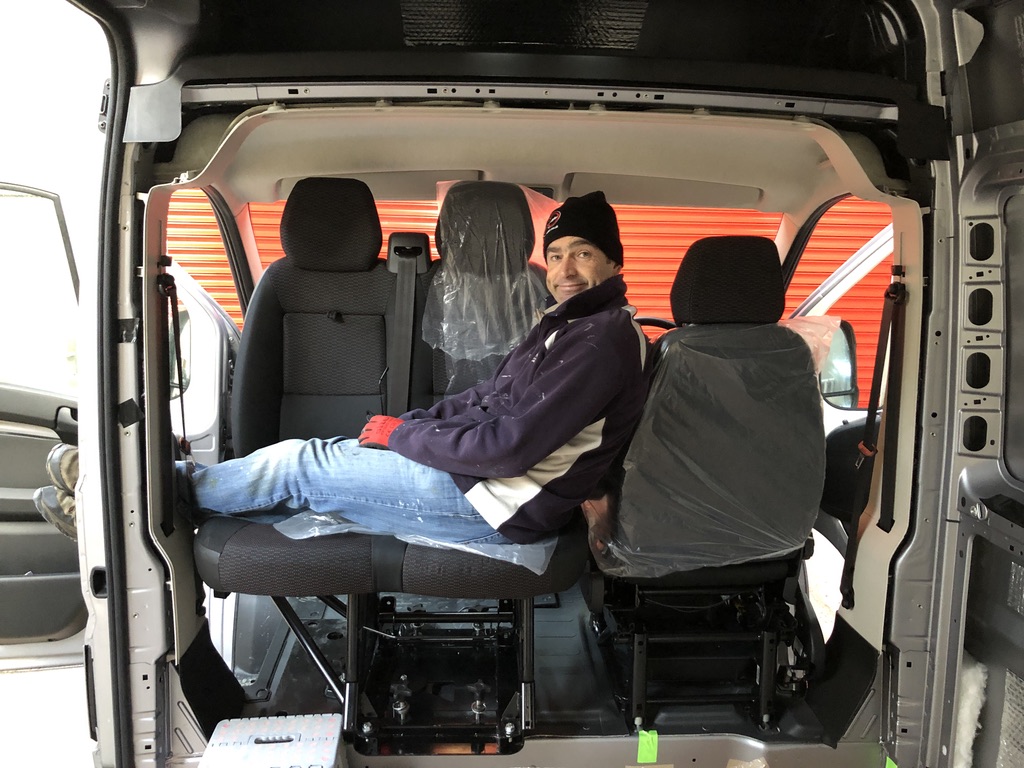
It’s a bit cumbersome and adds a bit of extra height to the passenger seat which means my feet can’t touch the floor, but it will do until we find a replacement single seat we can afford.
Ceiling battens & insulation
We used 15mm hardboard as battens widthways across the ceiling and glued and screwed them to the ribs of the van. We filled the ceiling with 40mm rigid insulation boards and sealed it all with aluminium foil tape to create a vapour barrier.
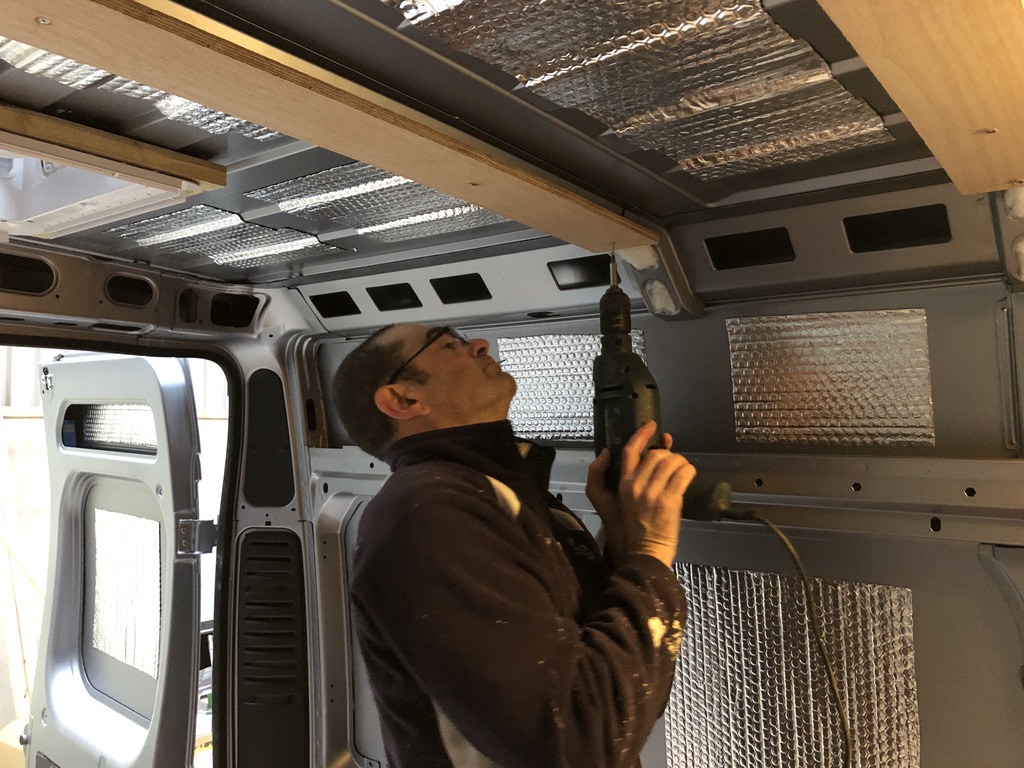
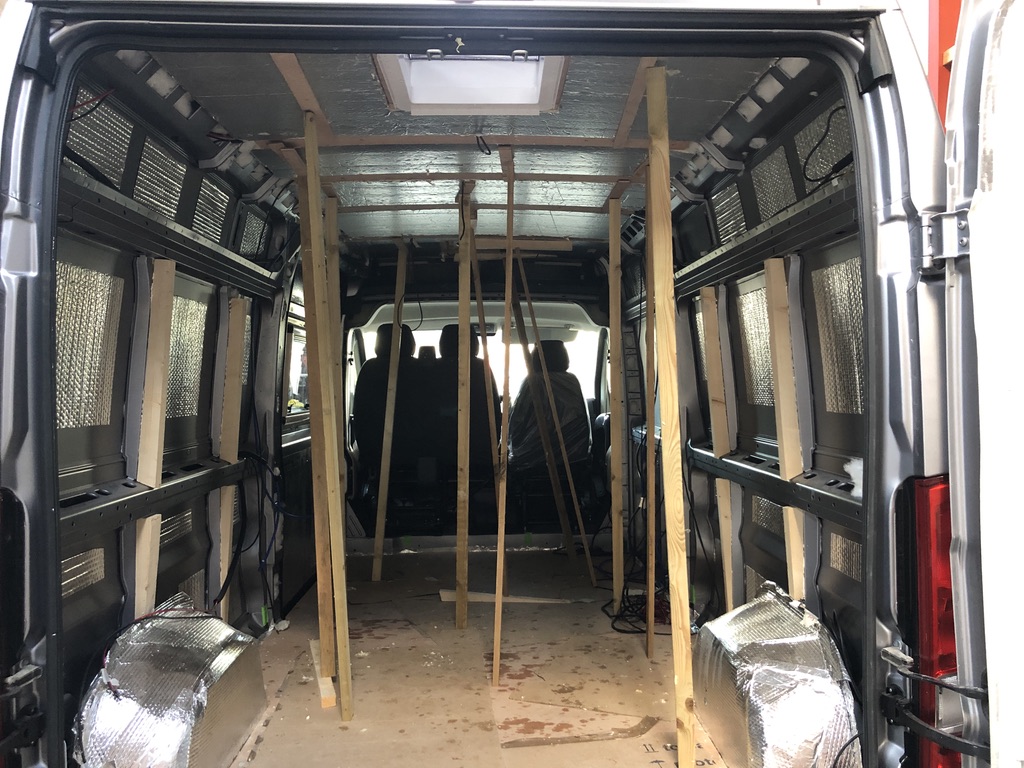
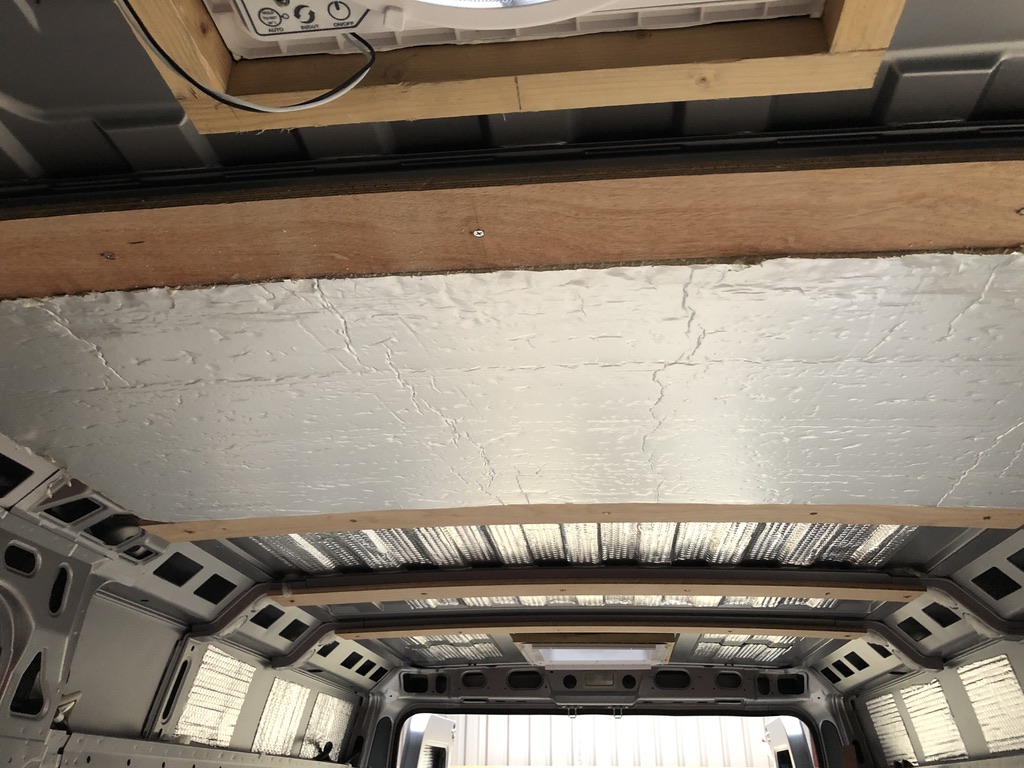
Installing a reversing camera & dash monitor
With no rear view mirror in the van, the reversing camera and dash monitor was an early priority for us. This was the first of many things we ordered only to find when they arrived they were not the items we ordered! Anyway when we did eventually receive the right camera, the installation was pretty straight forward. Although we have to admit it was a little scary when faced with the van fuse box and the decision of which wire to cut!
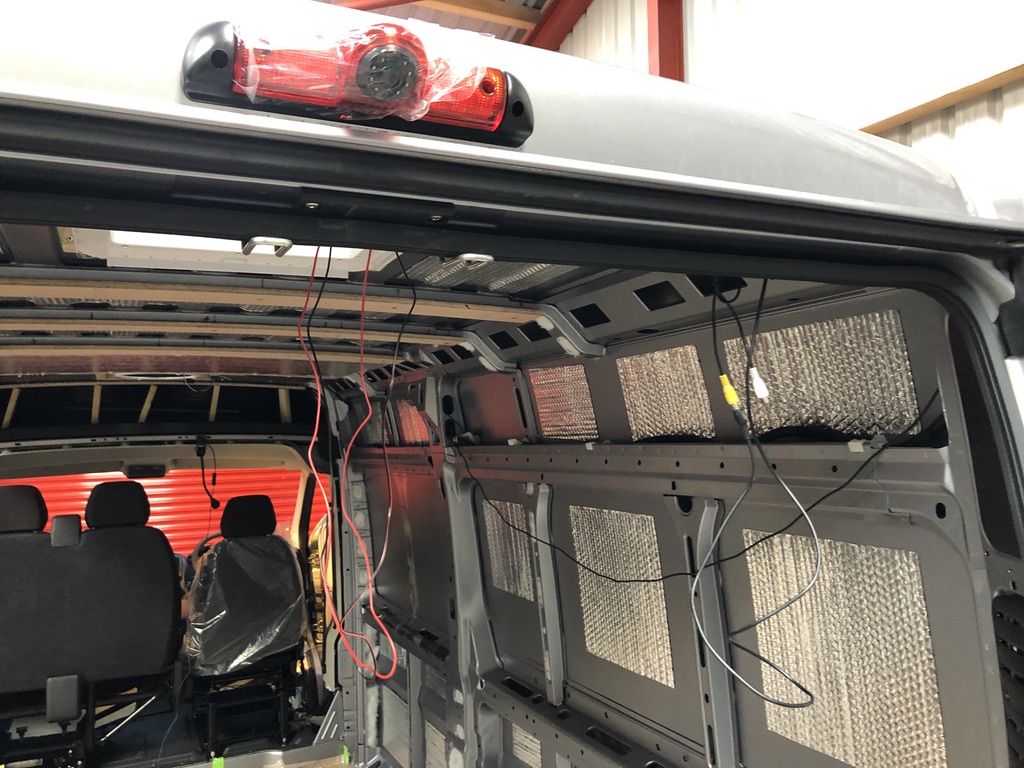
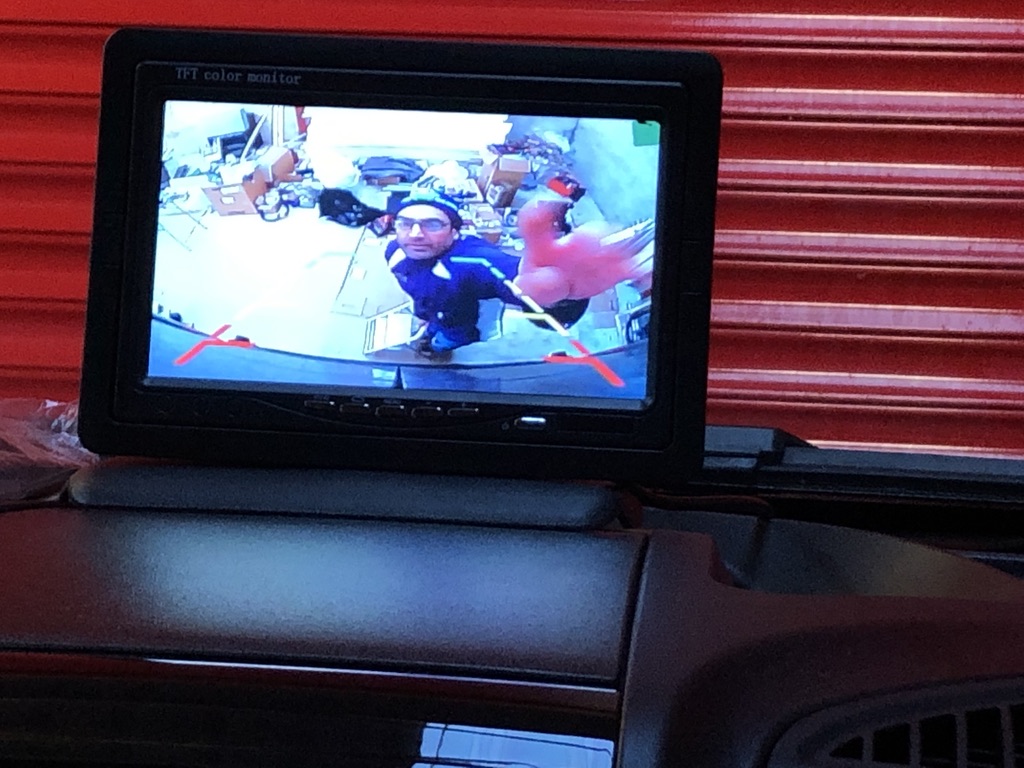
Electrical System – first fix
The next stage in our van build process was to do the first fix electrics so that all the cables and wires could be in place and hidden before we started ply-lining the van.
Our primary aim was to design and install a 12v and 240v electrical system as well as a solar power system so we could live off-grid. This is where being members of the Self Build Motor Caravanners Club came into it’s own. Dave was able to draw up a diagram of our planned electrical system and get feedback from some of the experts in the group before we started running cables and wires through the sides and roof of the van.
We have to say the folks at 12 volt planet where we bought the majority of our wiring products were also very helpful, and the expertise from Alpha Batteries was invaluable when choosing our lithium battery.
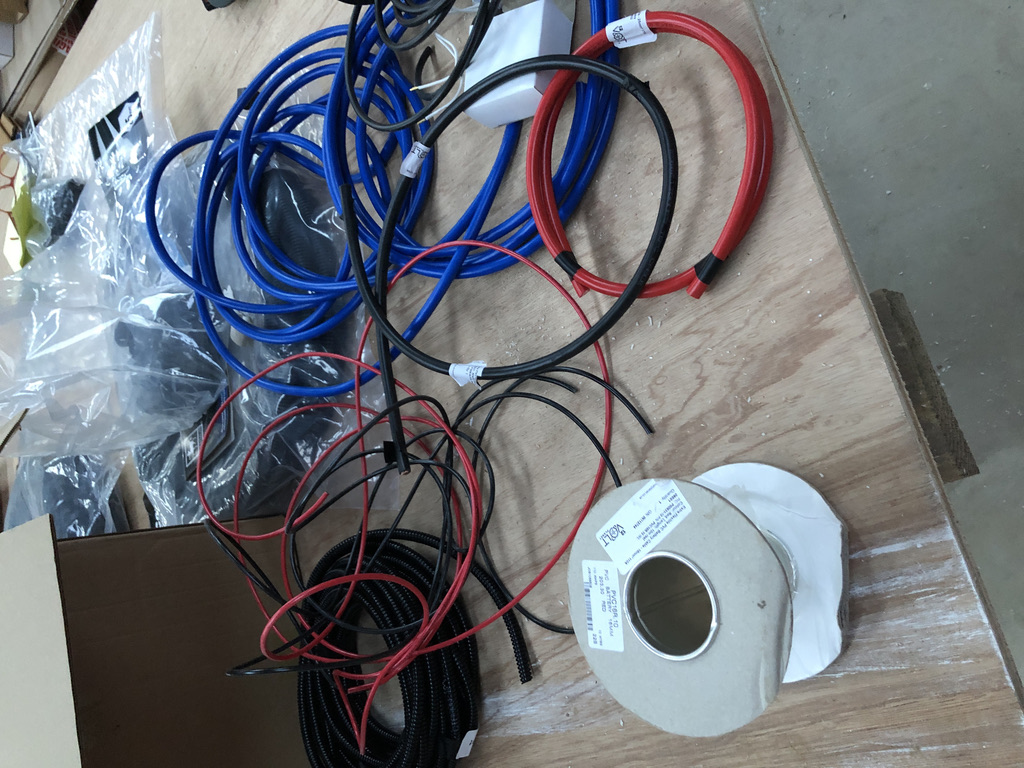
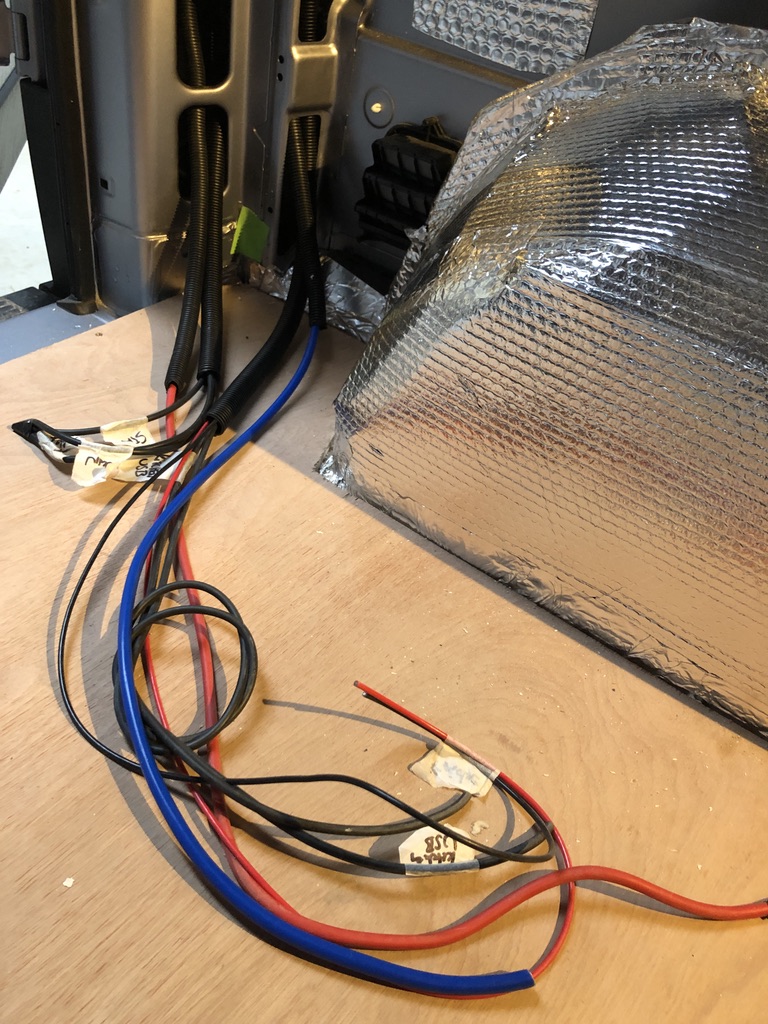
Rear doors
We used rolls of recycled plastic bottle insulation to fill all the gaps in the doors. We lined them with Dripex double aluminium bubble foil insulation sealed with silver tape to create a vapour barrier. We cut the rear door panels from 6mm plywood and used a router to create a tongue and groove effect on the upper half of the panels.
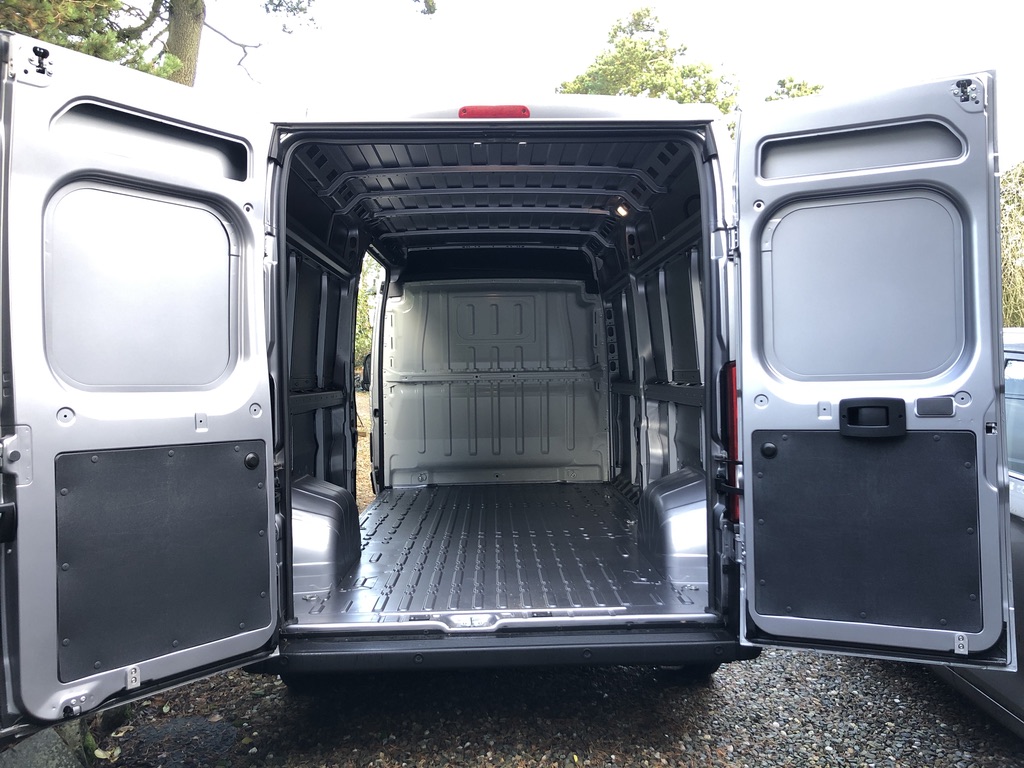
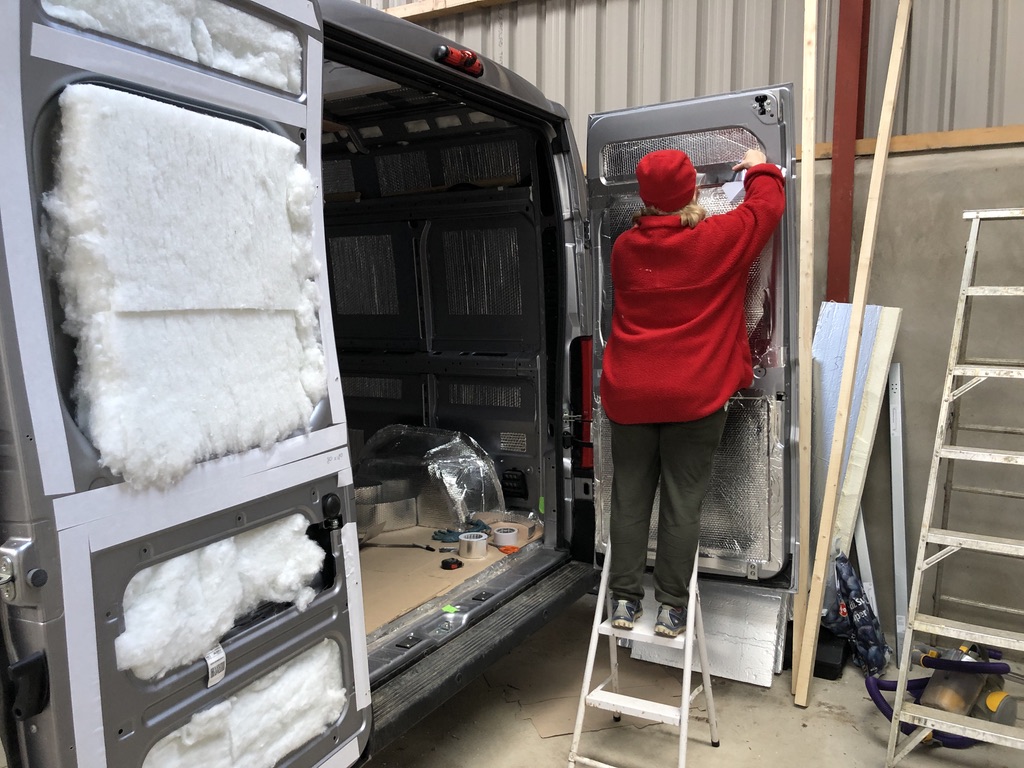
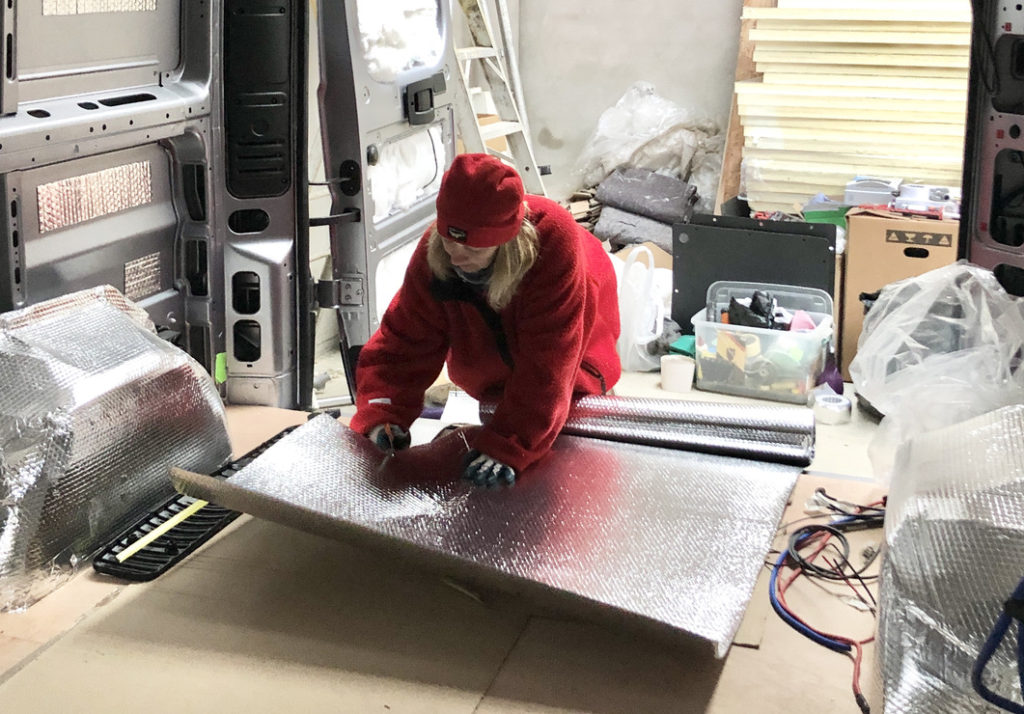
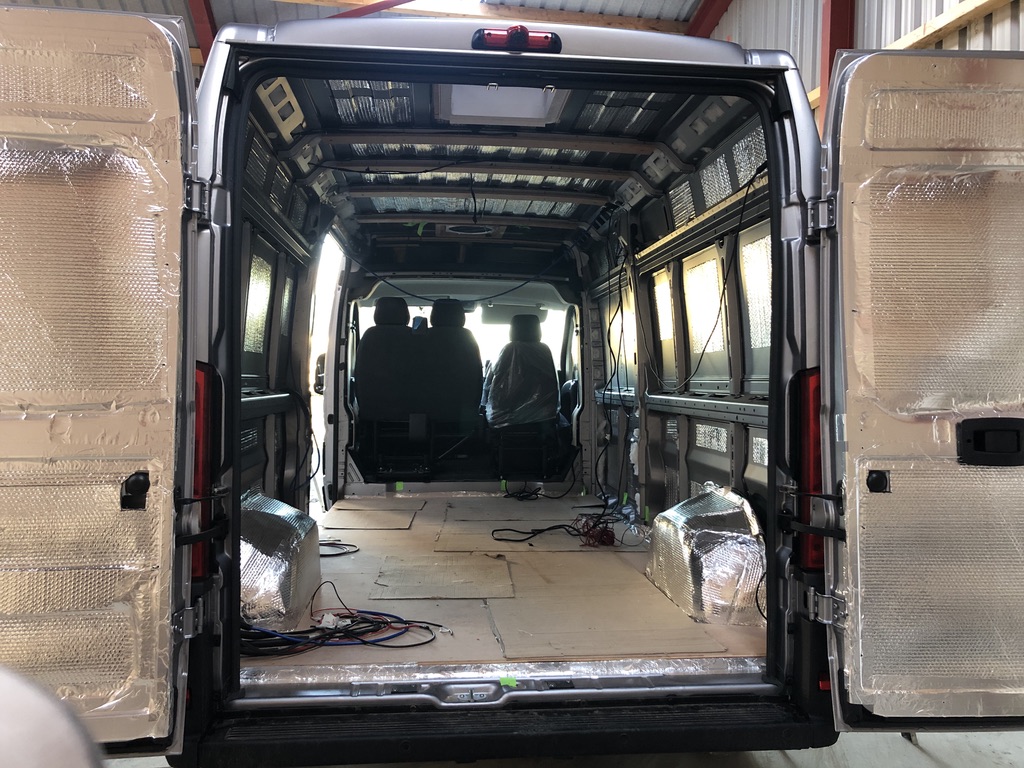
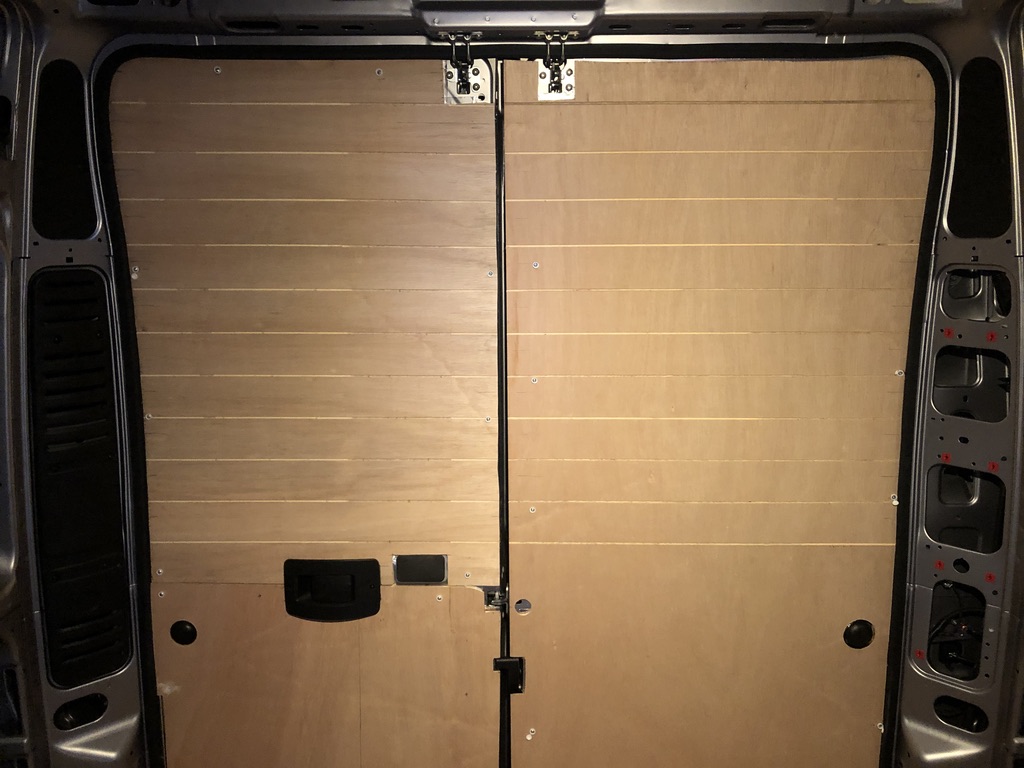
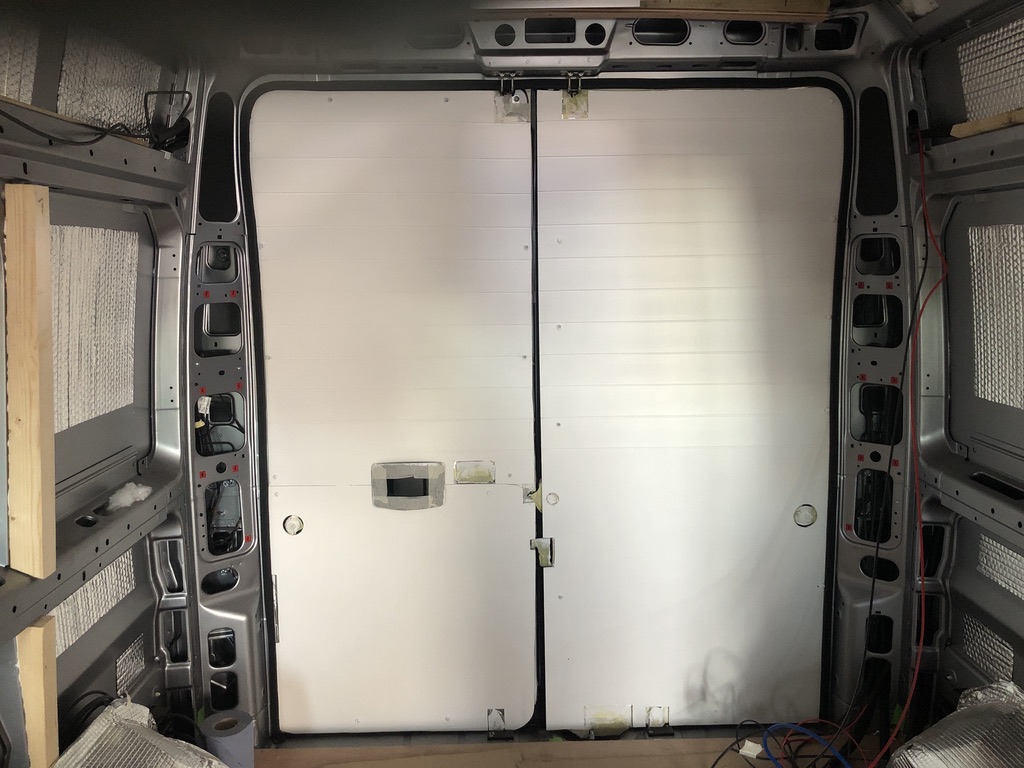
Walls
The same recycled plastic bottle insulation as in the doors was used to fill the wall cavities before we glued the timber battens to the ribs of the van. We screwed in extra reinforcements on the bed area – you never know it might see a bit of action!!! We covered the insulation from top to bottom with the Dripex silver bubble foil and once again sealed that with silver tape to create the vapour barrier. What was a tin can van was now starting to look more like a silver spaceship!
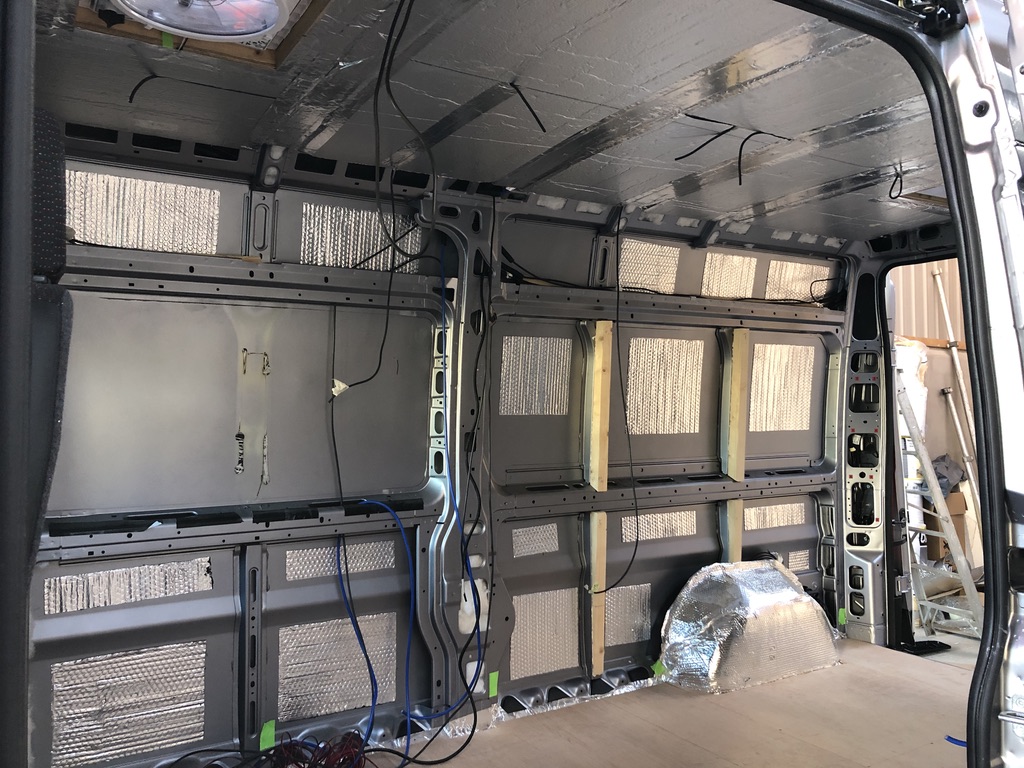
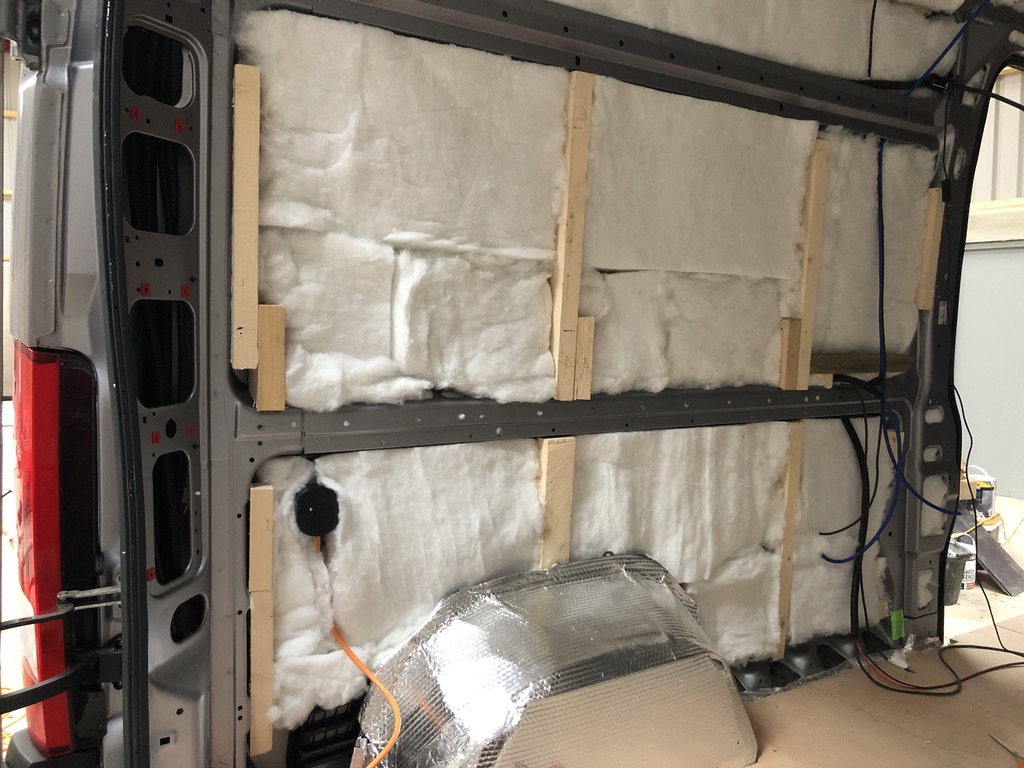
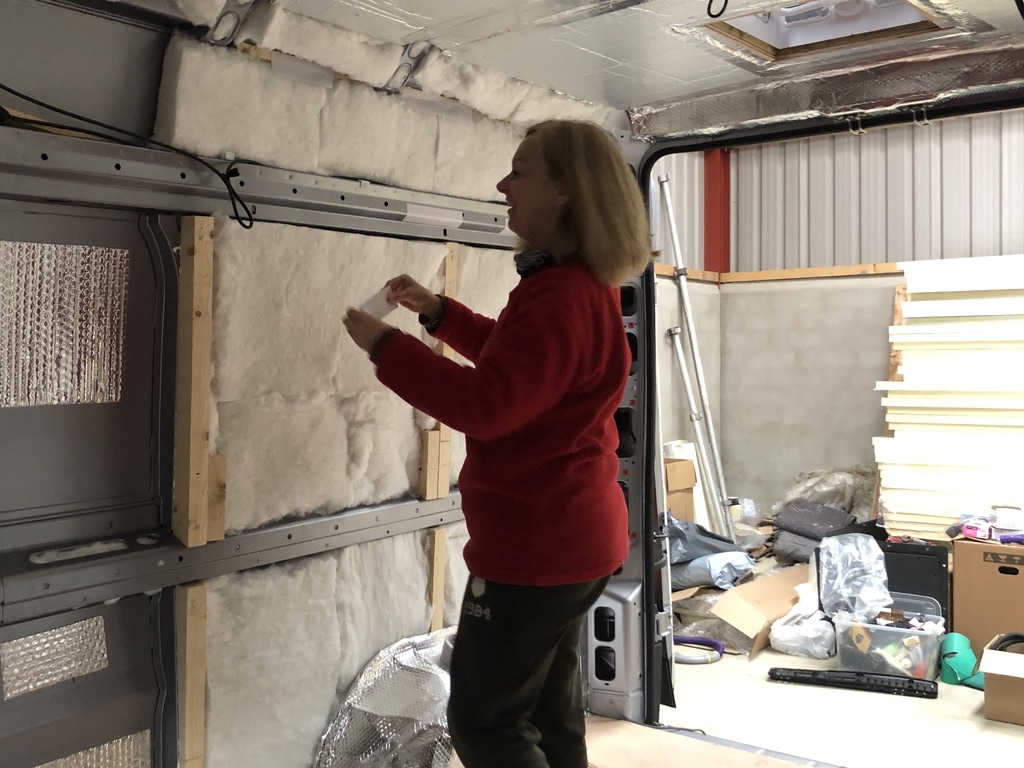
We cut our wall panels from 9mm plywood, and they took a bit of fitting and refitting after we realised we’d put a couple of the kitchen electrical cables in the wrong spot!
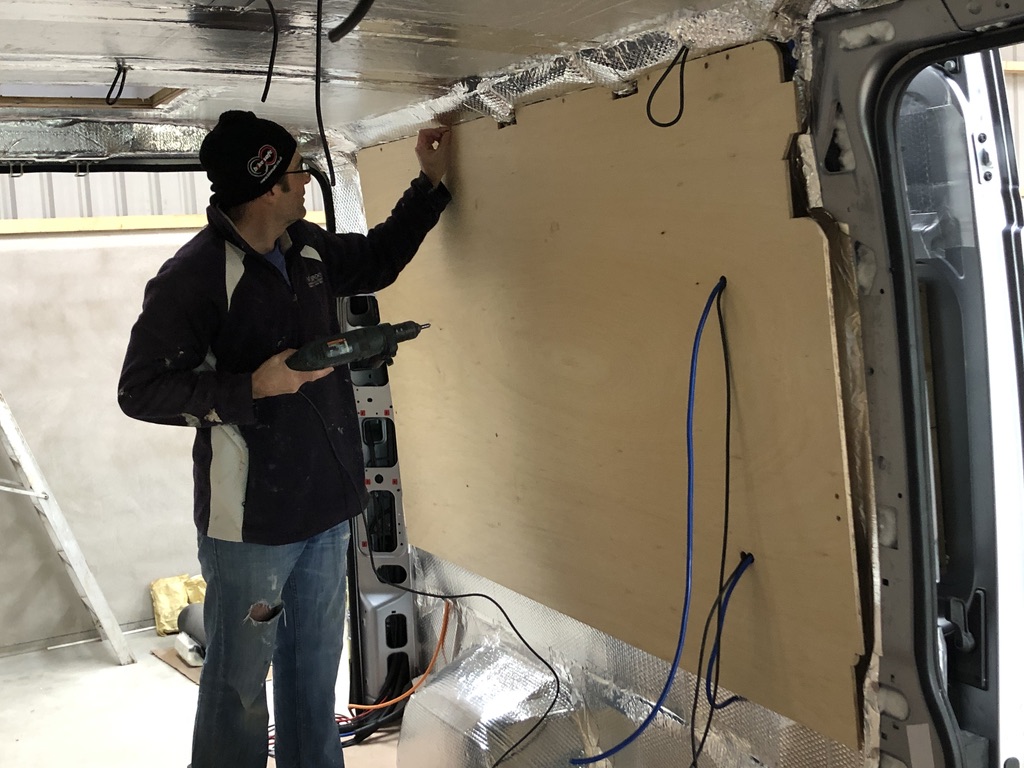
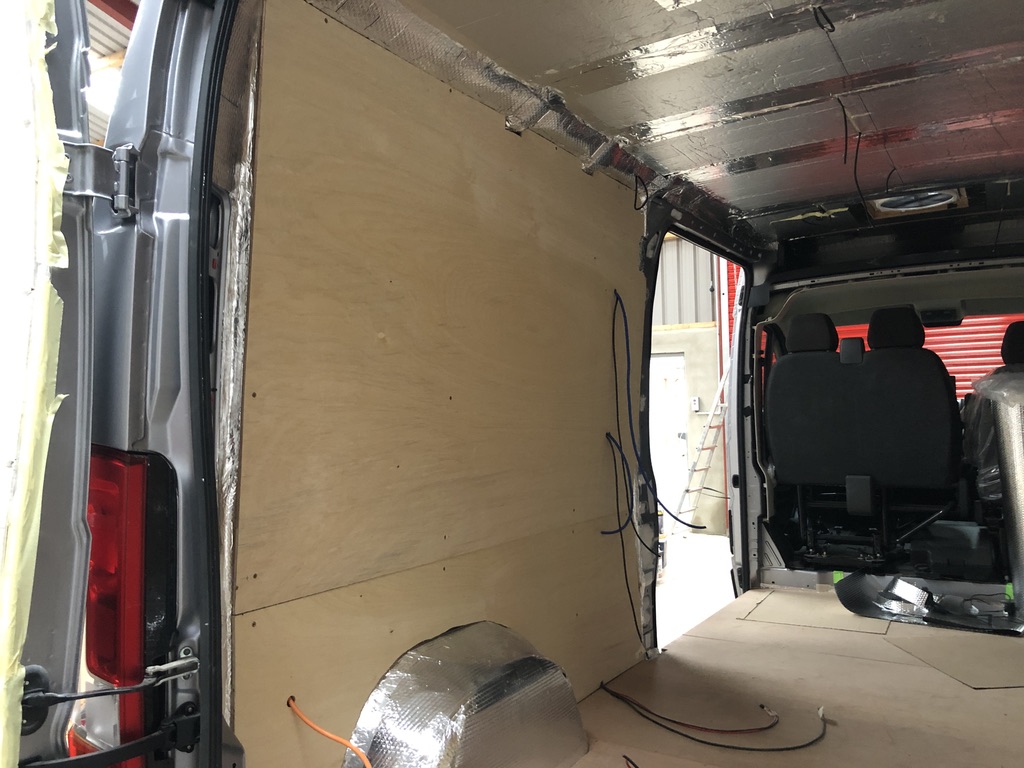
Wheel Arches
A relatively simple job in the scheme of things was to cover the wheel arches and box them in using plywood. The tops are removable so we can easily access the tyre jack tool kit stored in there.
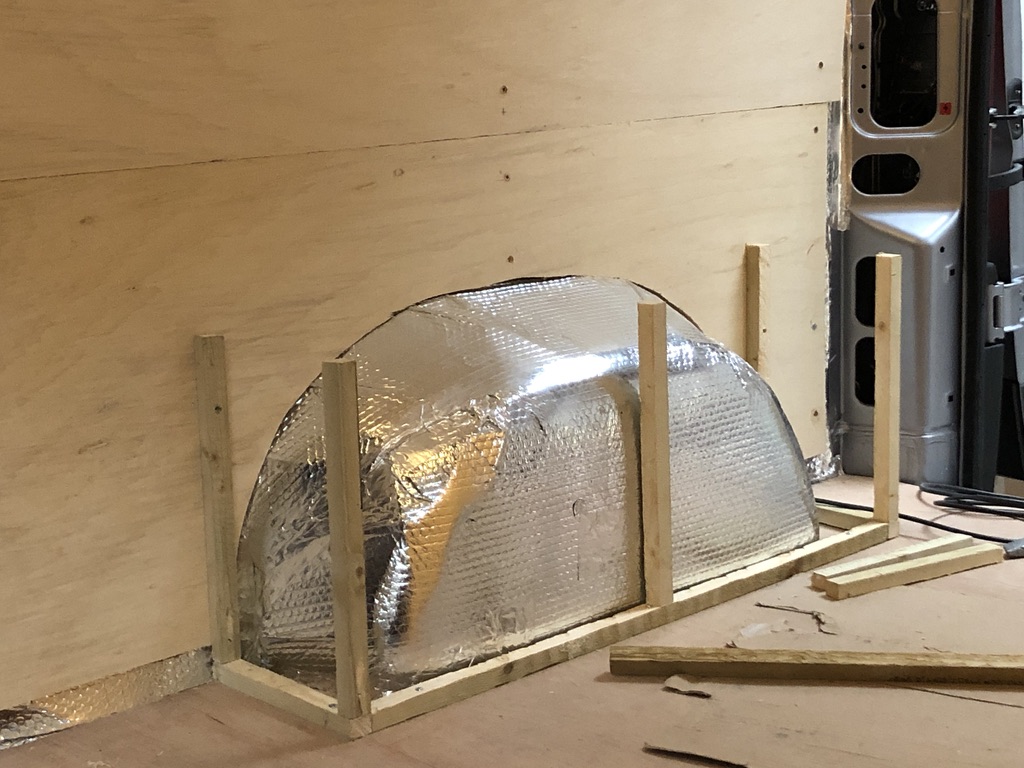
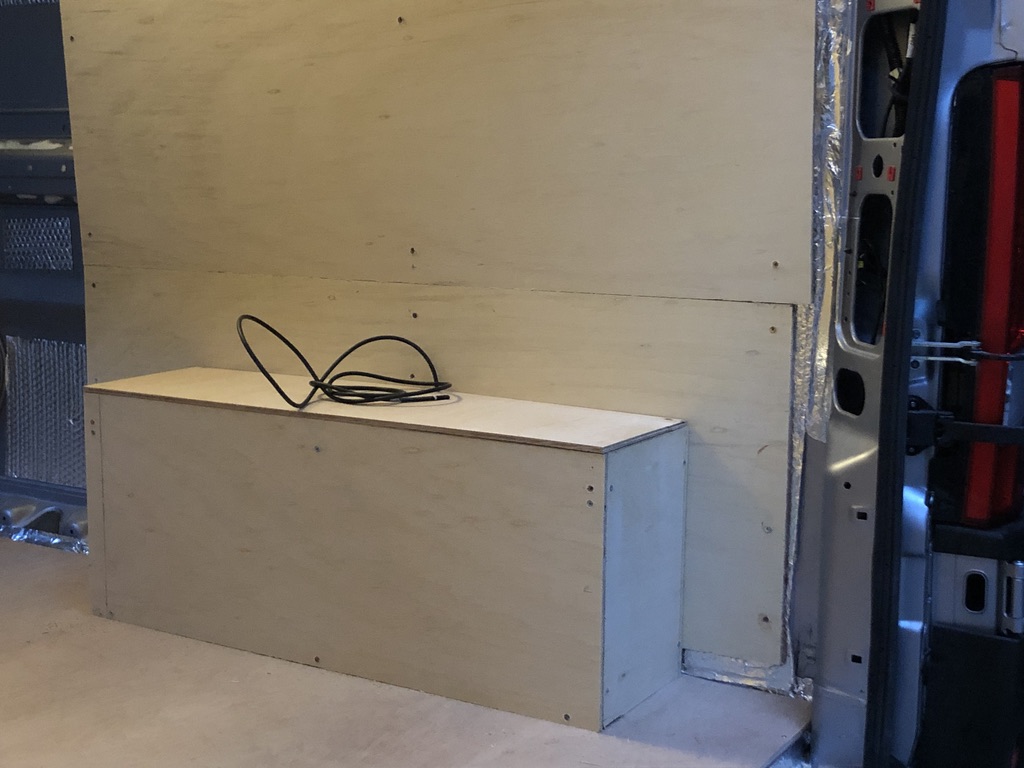
Bathroom window
Time to cut another hole in the van! Instead of an extractor fan we opted to fit a tinted side slider window for our bathroom. We had it custom made (350mm x 180mm) by Caldwells Windows.
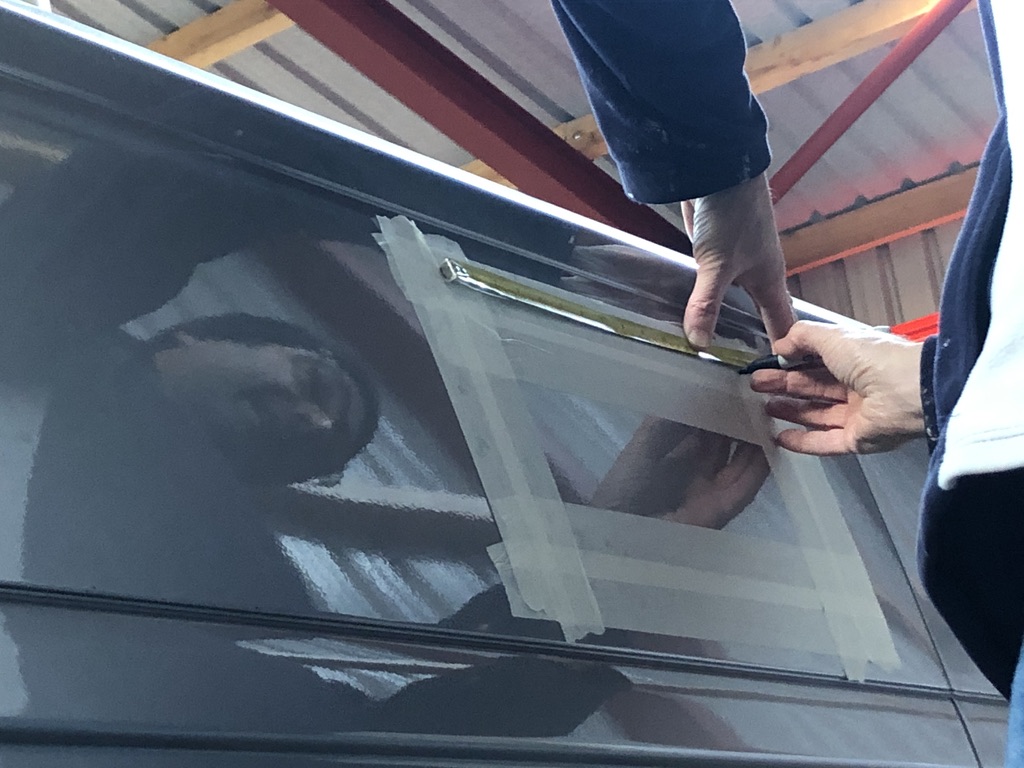
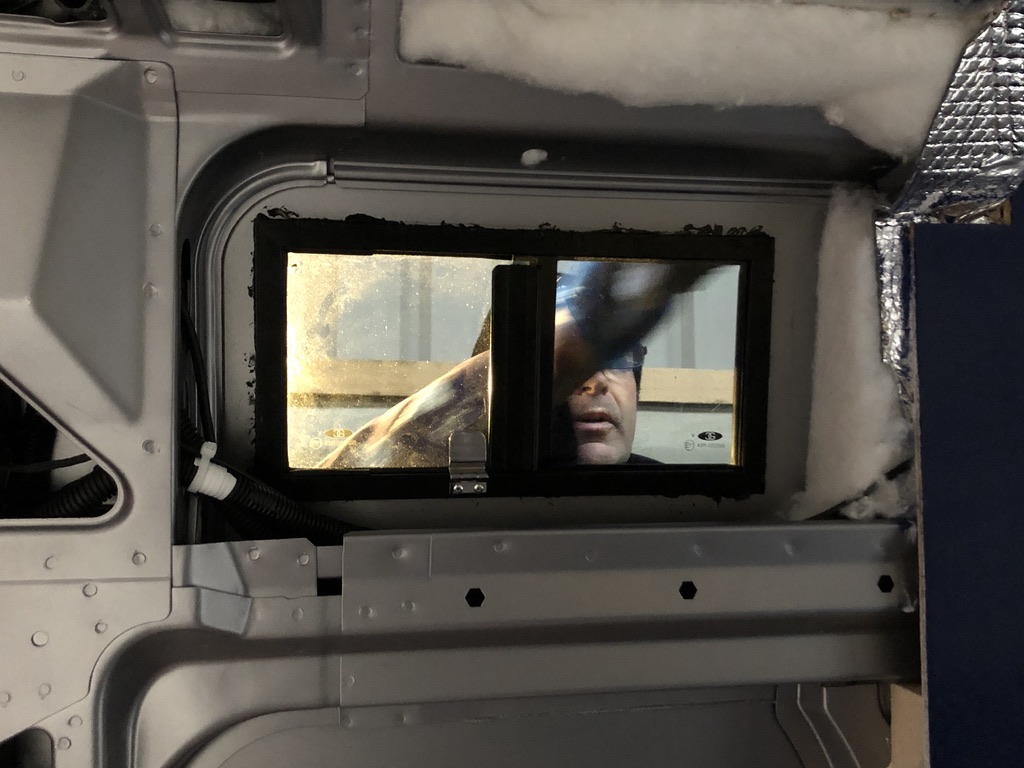
Garage
We laid the top floor in the garage (the storage area under the bed) using vinyl peel and stick tiles from B&Q. Every millimetre is important when it comes to your van build and these tiles were as thin and practical as we could find.
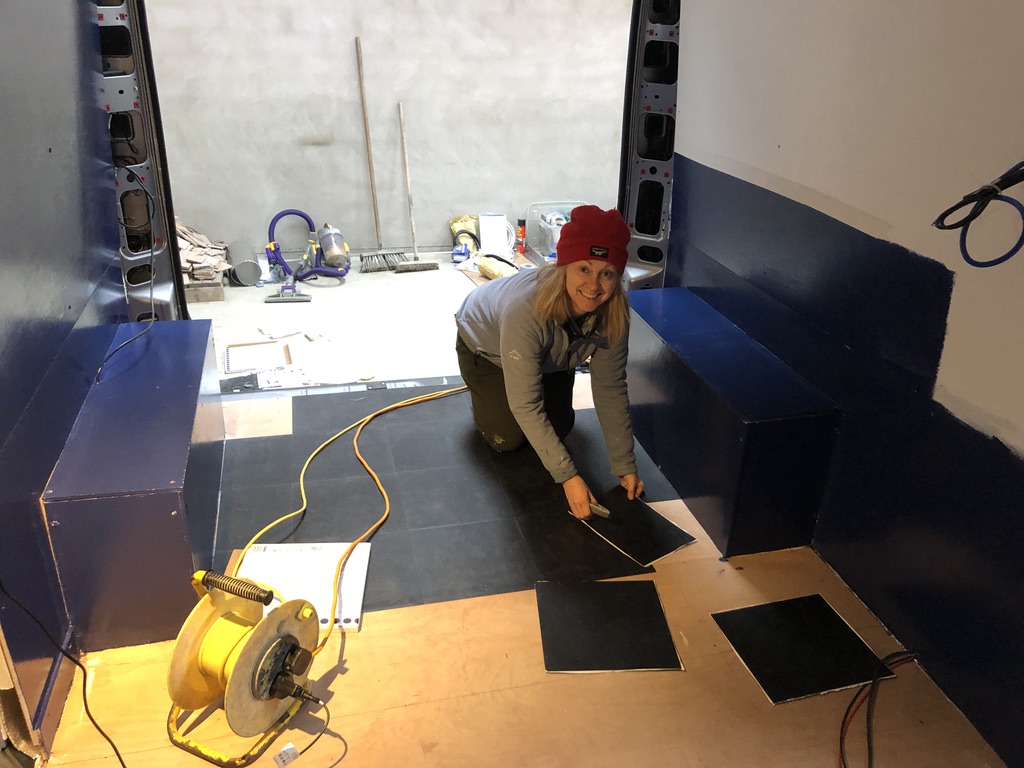
One of our essential requirements for the van build was that our bikes were stored inside the van for security & protection, but be easily accessible. At a later stage of the build we would add a slide out tray in the garage for the bikes.
Ceiling cladding
We’d prepared the tongue and groove boards by sanding, priming and painting them earlier in the build process. It was much easier to do this in the large open space of the shed rather than try and do it after fitting them. Doing it once they were fitted would’ve meant so much dust in the van and a lot or arm and shoulder ache from working above your head! Finding the right size white head screws for fitting the T&G was another task that took hours trawling online. Once the cladding was secured we were able to fit the covers and trims to the roof fan and sky light.
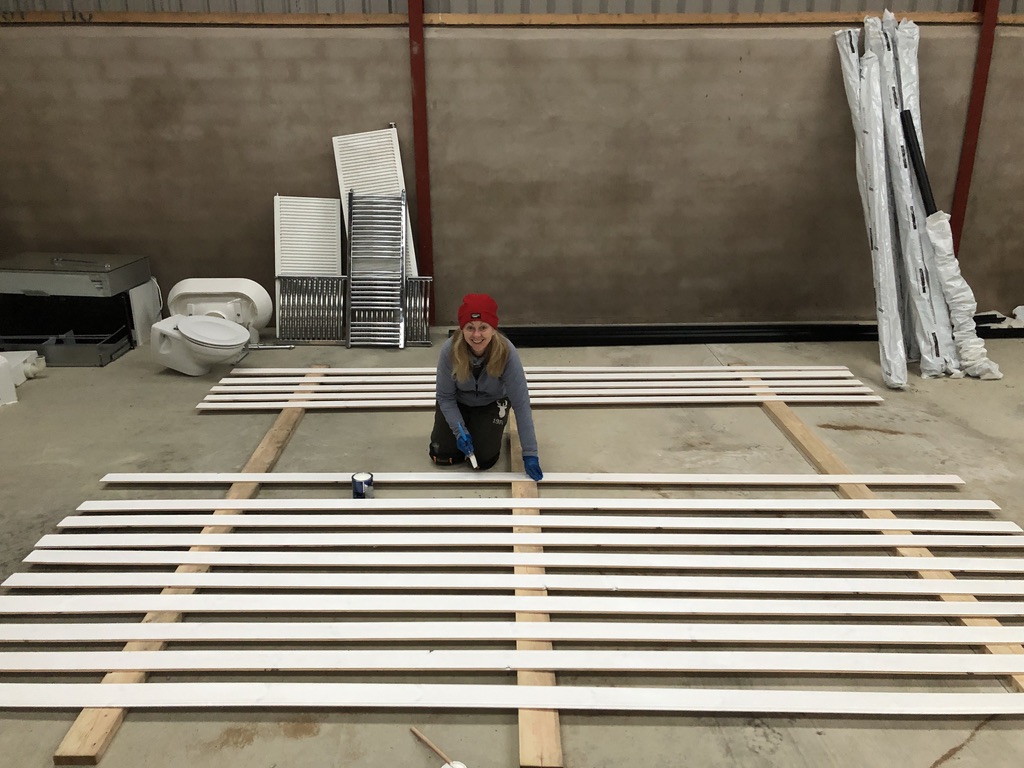
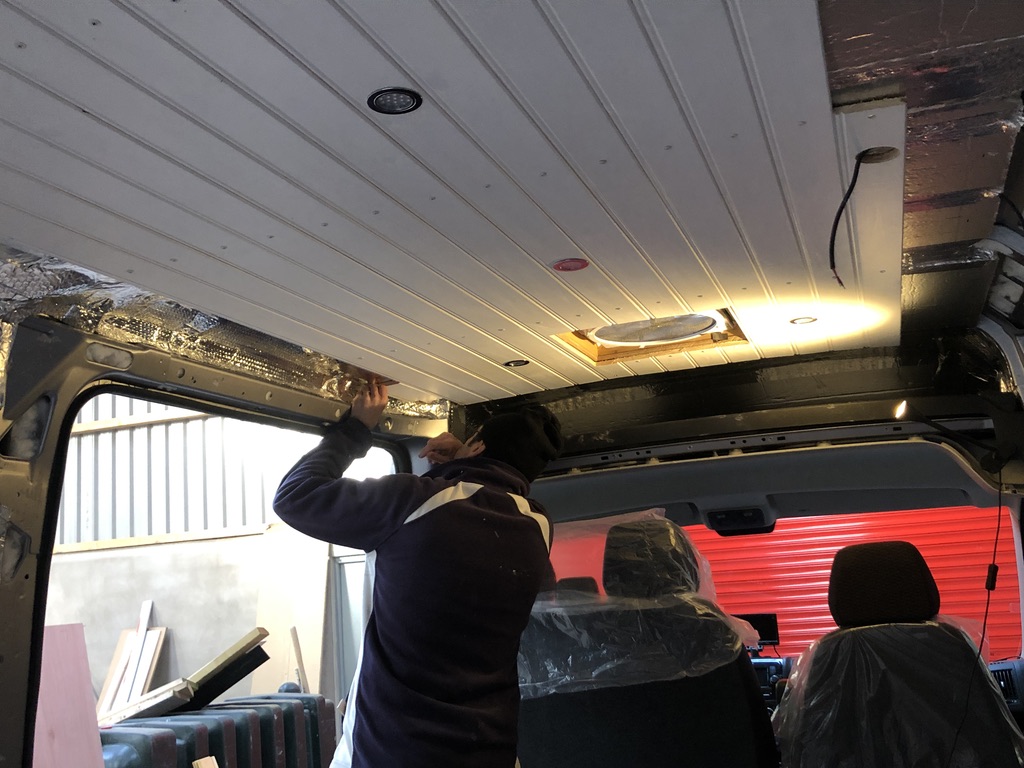
Lighting
We fitted seven touch sensitive recessed 12v LED lights in the ceiling (3 in the lounge area, 3 in the kitchen and 1 in the bedroom) that we sourced online from Vanwurks. Plus two 12v LED flexible reading lights above the bed area.
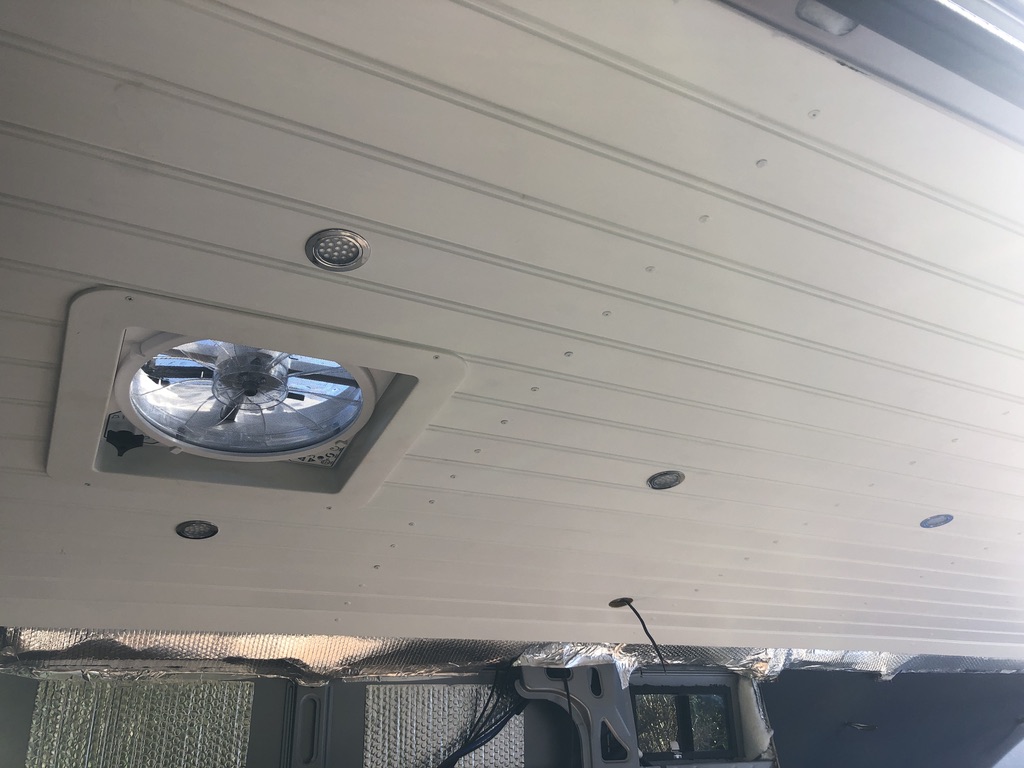
Painting
This first painting stage gave the van a new lease of life. We used brilliant white on the walls and ceiling, and Dulux Sapphire Salute as a feature colour on the bed head.
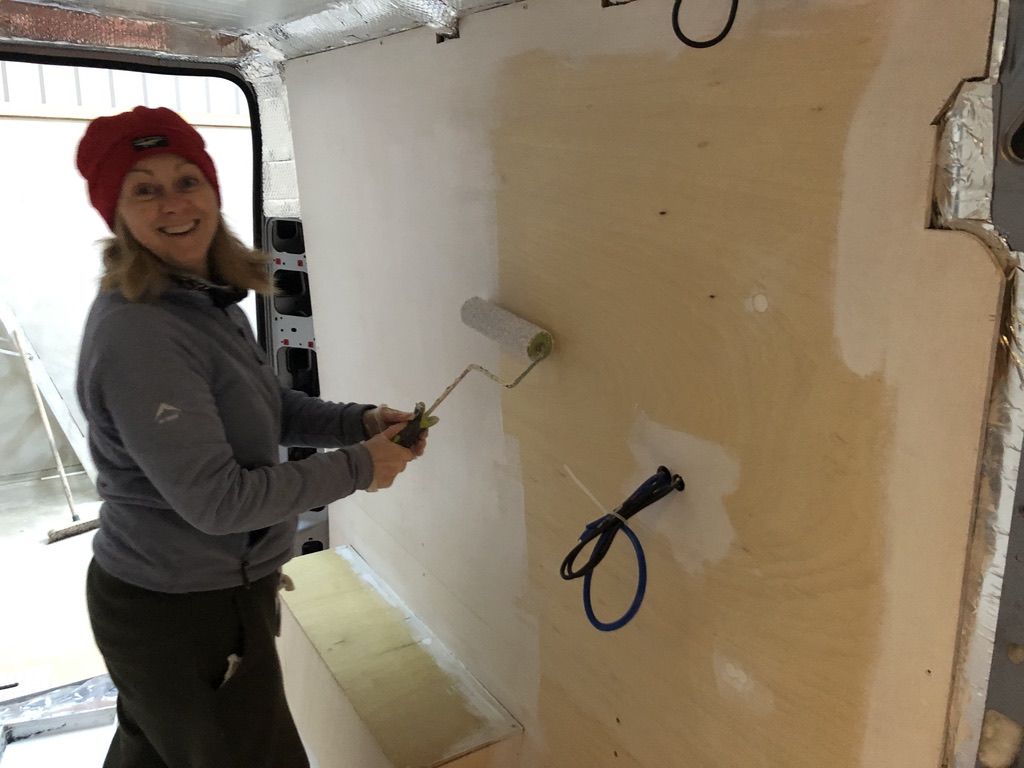
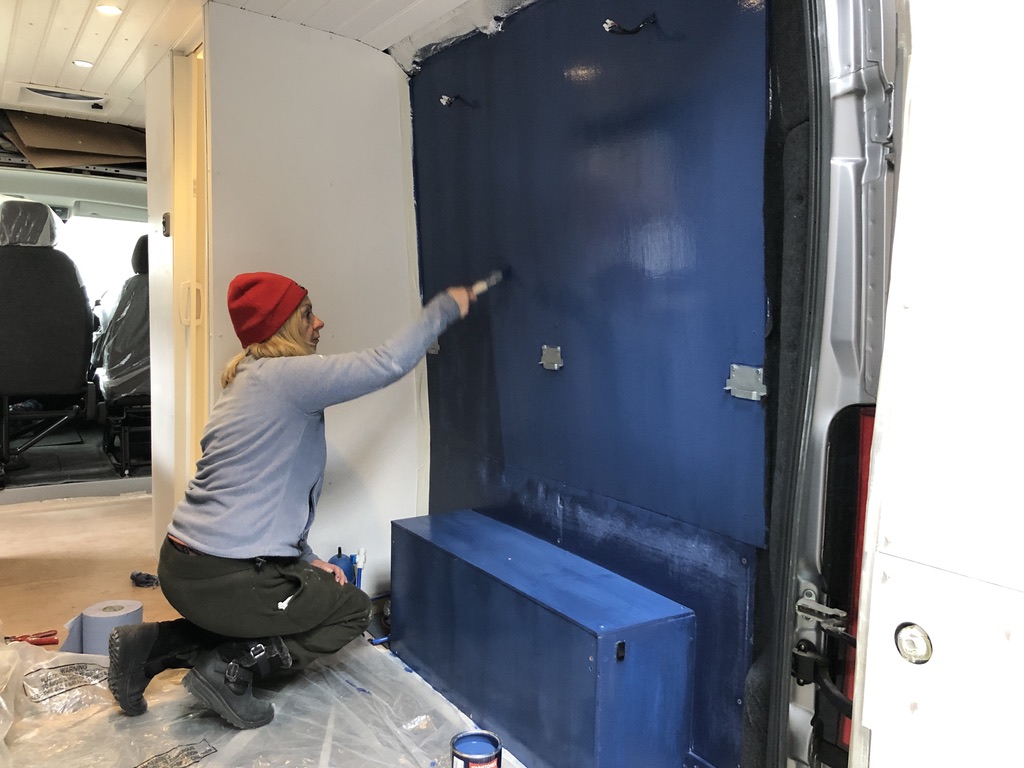
Electrical System – wiring
By week 8 of the build we, or rather Dave, was ready to wire up the 12v and 240v electrical system. Our system components, housed in the garage area, included a 200 amp hours lithium battery, a Victron MPPT solar charger controller, a Sterling battery to battery charger, the 230v hook up, a consumer unit/fuse board, a Victron Blue power battery charger, and a Victron Energy 1200W Inverter. Plus we had the Longi 370W split cell solar panel already bolted to the roof.
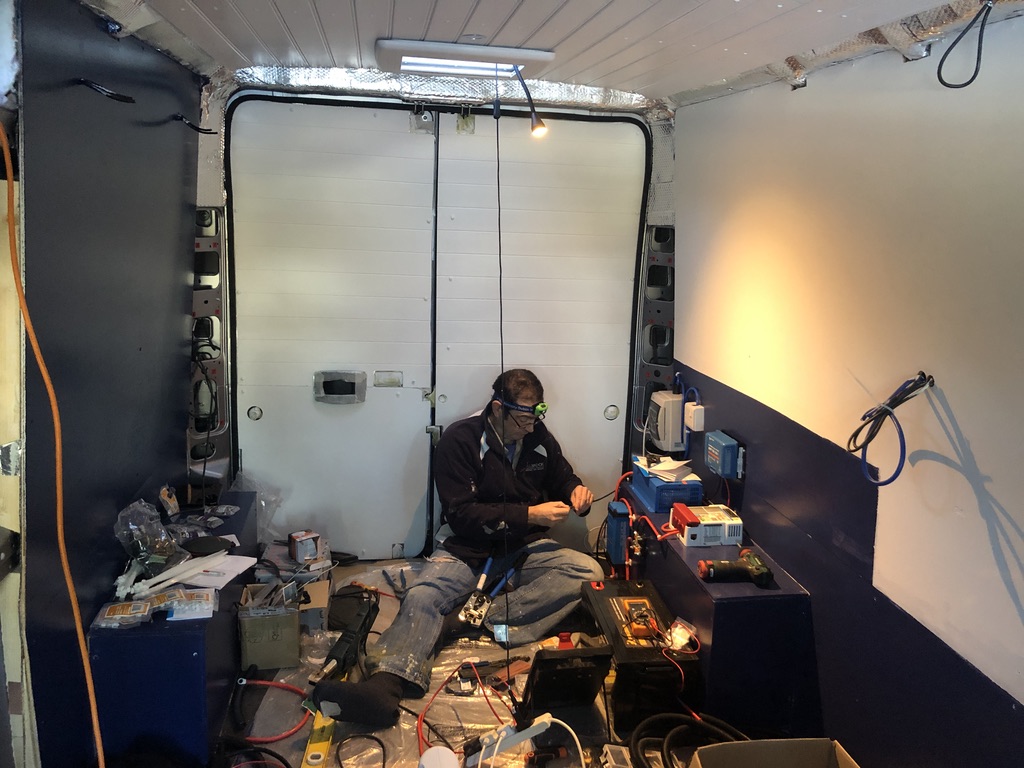
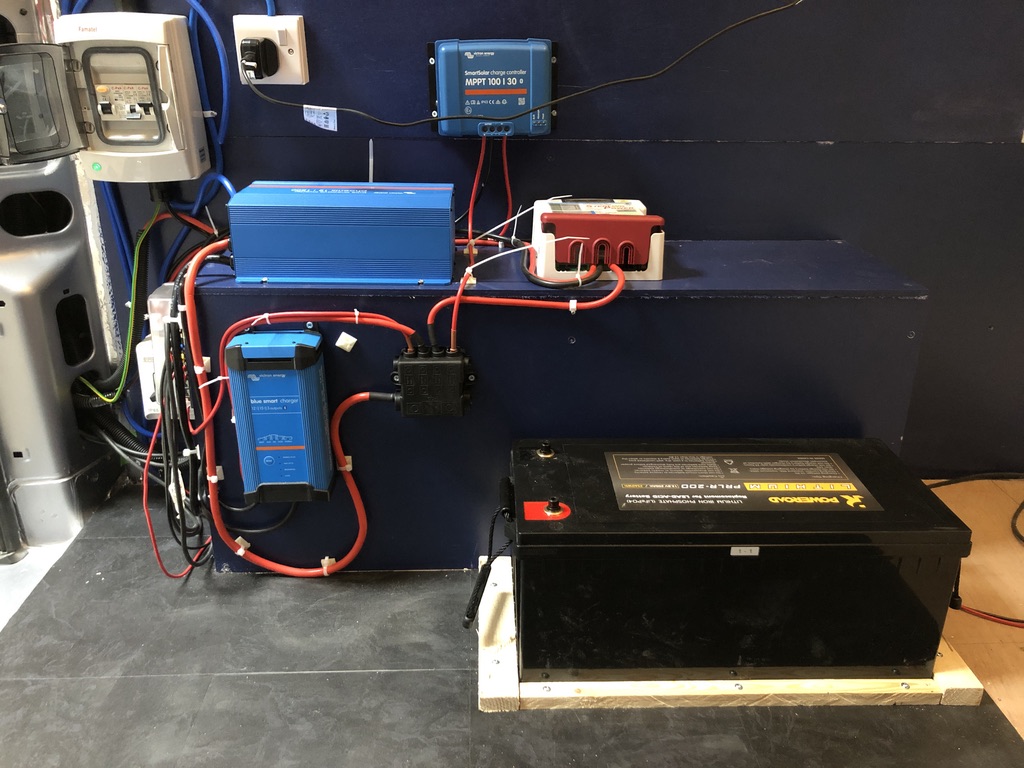
For peace of mind we had a local professional electrician complete a check up and reassure us it was all safe.
Plumbing & Heating
The next step was to get the plumbing and heating system in place. Earlier in our design process we had made the decision to go for underslung water tanks in order to save as much space on board as possible. We knew it was a long waiting list to get the custom made plastic tanks (82 litres fresh water tank and 63 litres waste water tank) from the very helpful Shaun at Barratts Tanks.
We ordered in October 2020 and had we been able to travel to England we could have had the tanks fitted in the December. We couldn’t travel due to Covid restrictions. Instead we had no choice but to have them delivered to us in Northern Ireland at the end of February 2021. We fitted them ourselves with full instructions from Shaun.
Before the tanks arrived we fitted the water pump, filter and accumulator, and installed the kitchen and bathroom water pipes and shower tap fitting.
At this point we also needed to finalise the positioning of our Truma Combi 4E gas boiler which we would use for space and water heating. We had changed our minds several times on the boiler position, eventually settling on the only really viable option which was under the sink. We positioned each of the heating vents – one in the bathroom, one in the lounge, one in the kitchen, and one under the bed in the garage.
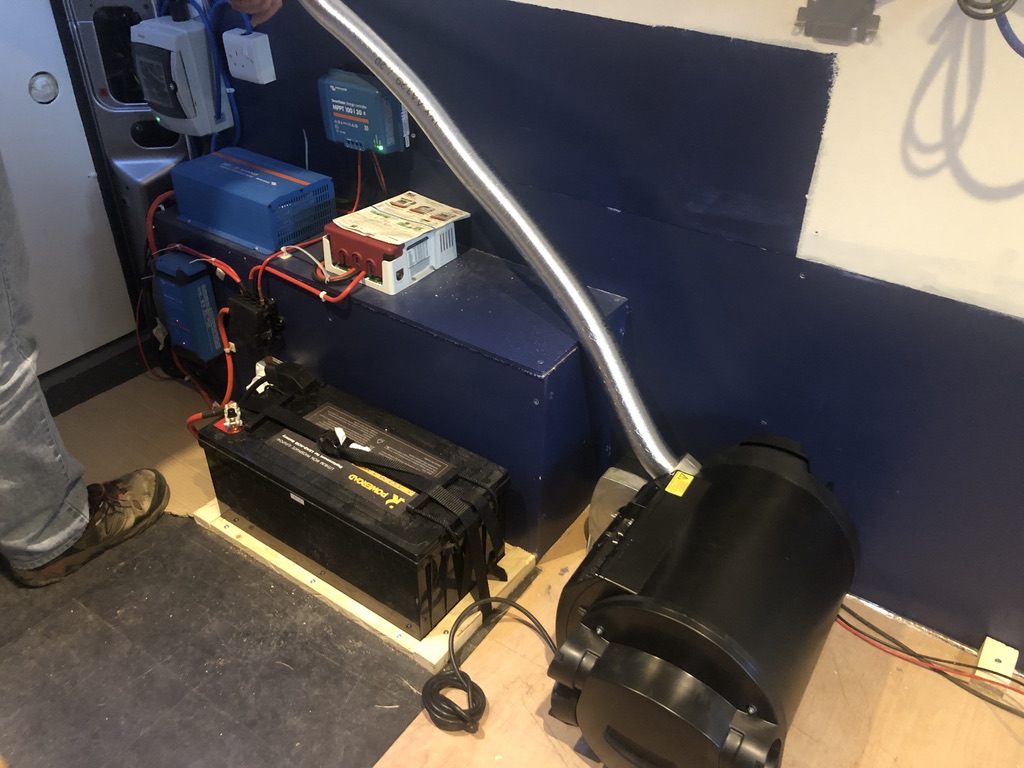
Bathroom
At only 610mm x 915mm the bathroom is not a big space, but a very tricky job to do!
The first stage was to build the wooden framework for the walls, followed by cutting and shaping 6mm plywood panels for the internal walls, and 9mm panels for the external walls.
Once the frame was in place we installed the fibreglass shower tray we sourced from Wesley Marine. The first pilot hole we drilled for the shower waste was not in the most accessible location, so after resealing that we had to drill another before we could connect the waste water pipe.
We covered the walls in white gloss PVC panels, made and fitted the window frame, and installed a waterproof ceiling light we found on E-bay. Fitting the PVC to the ceiling was a job that tested both of us to our limits. There are no such things as straight lines in a panel van!
We designed and built a simple separating compost toilet to fit on the shower tray using a wooden box framework with a regular toilet seat on top. We attached a we-pee urine separator to the underside of the toilet seat. Inside the box was a bucket for the solids and a 5-litre container for the pee. We covered the box framework with the same gloss PVC panels as the walls.
The final piece of the bathroom build was cutting the folding door to size.
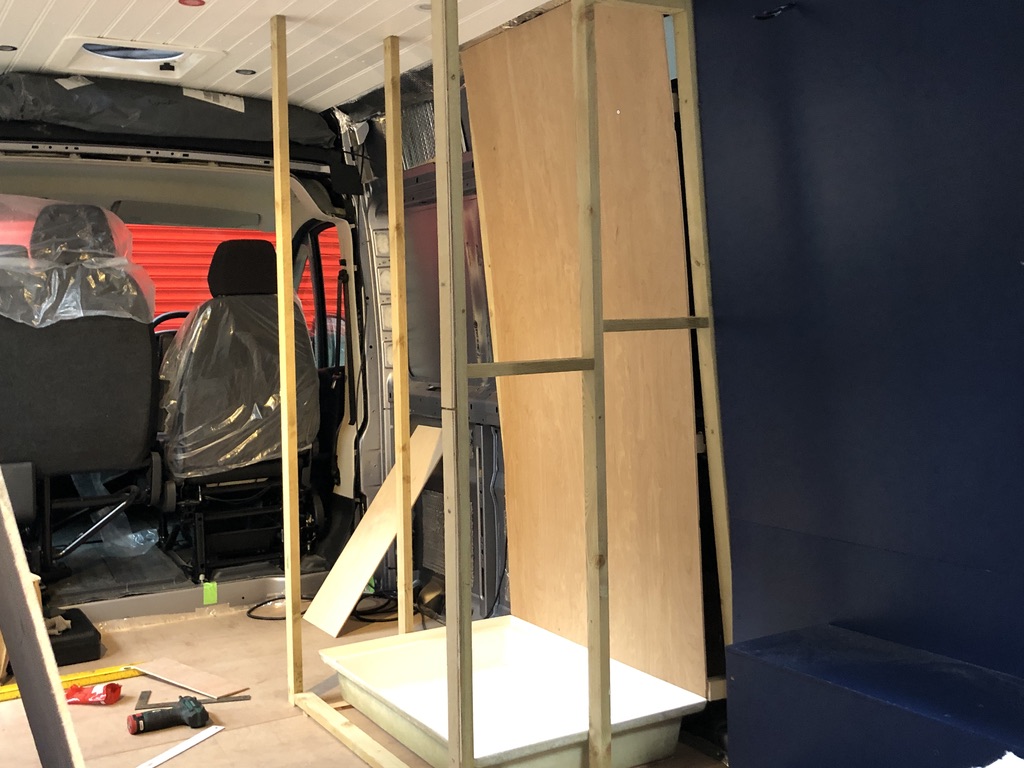
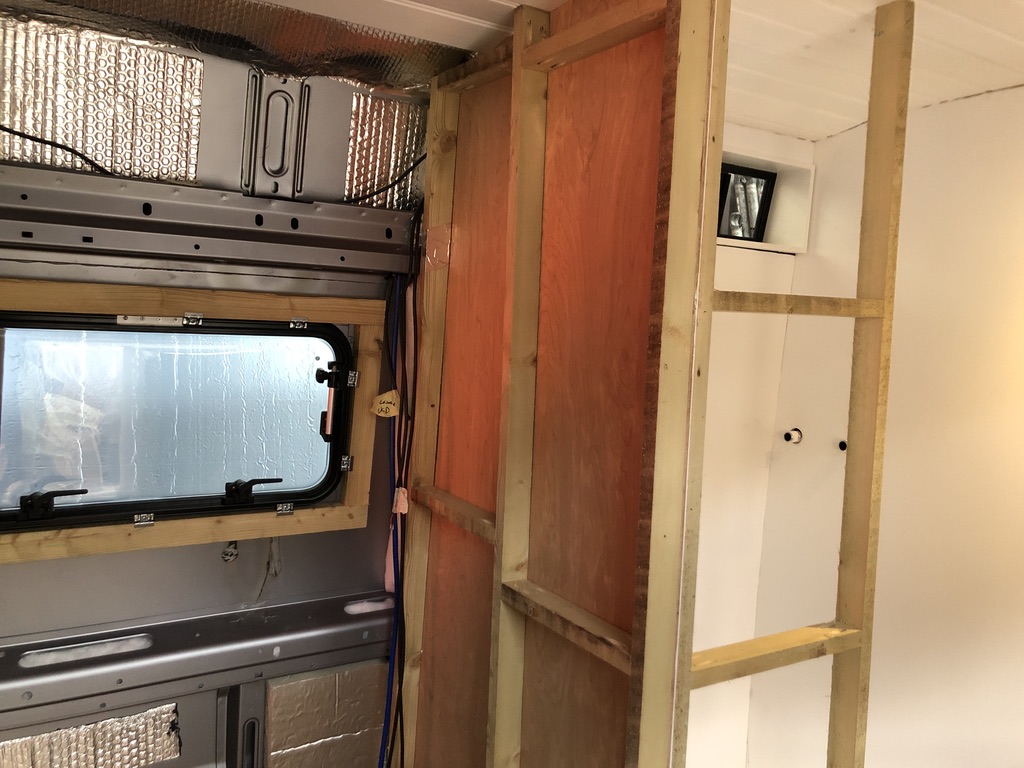
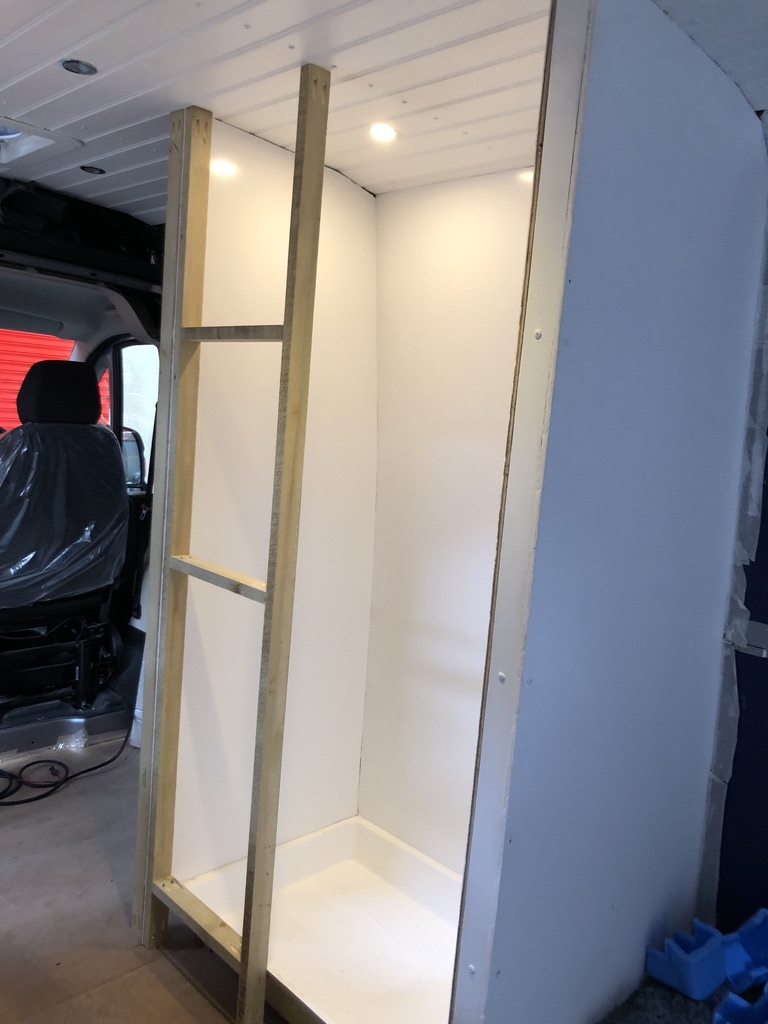
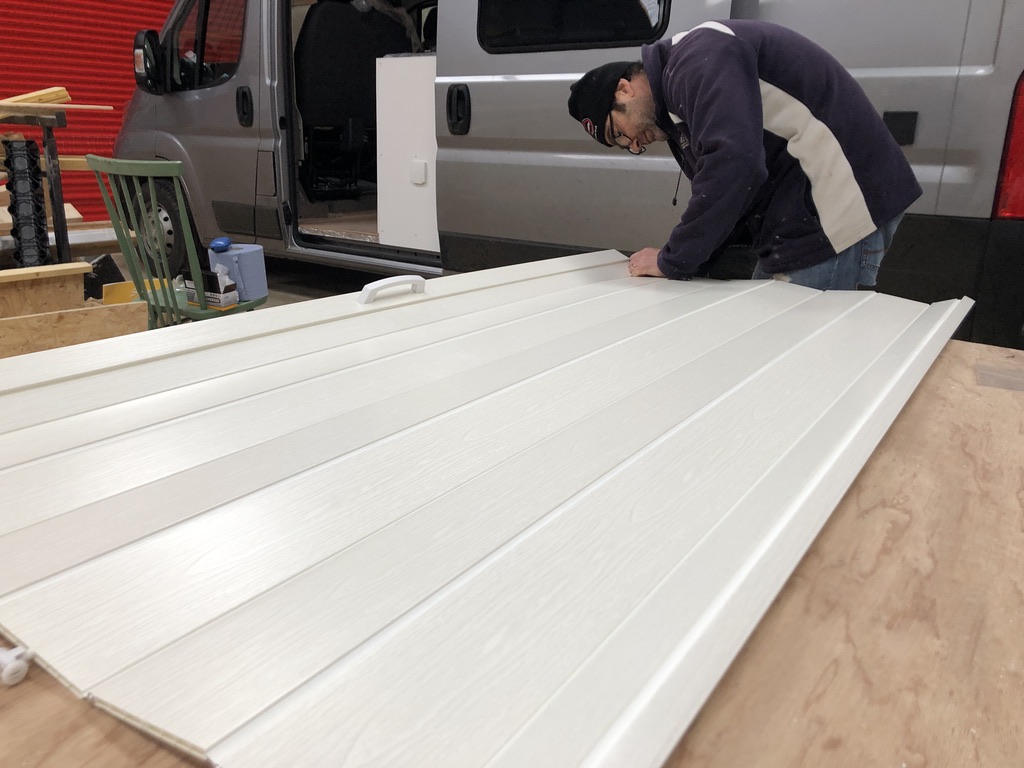
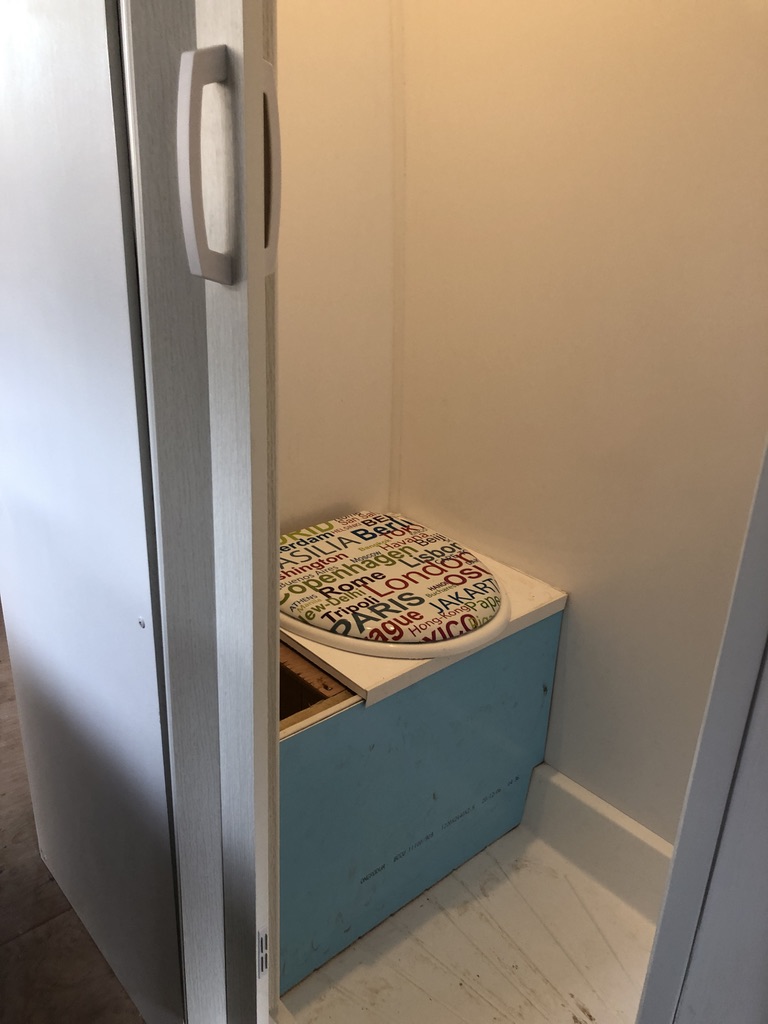
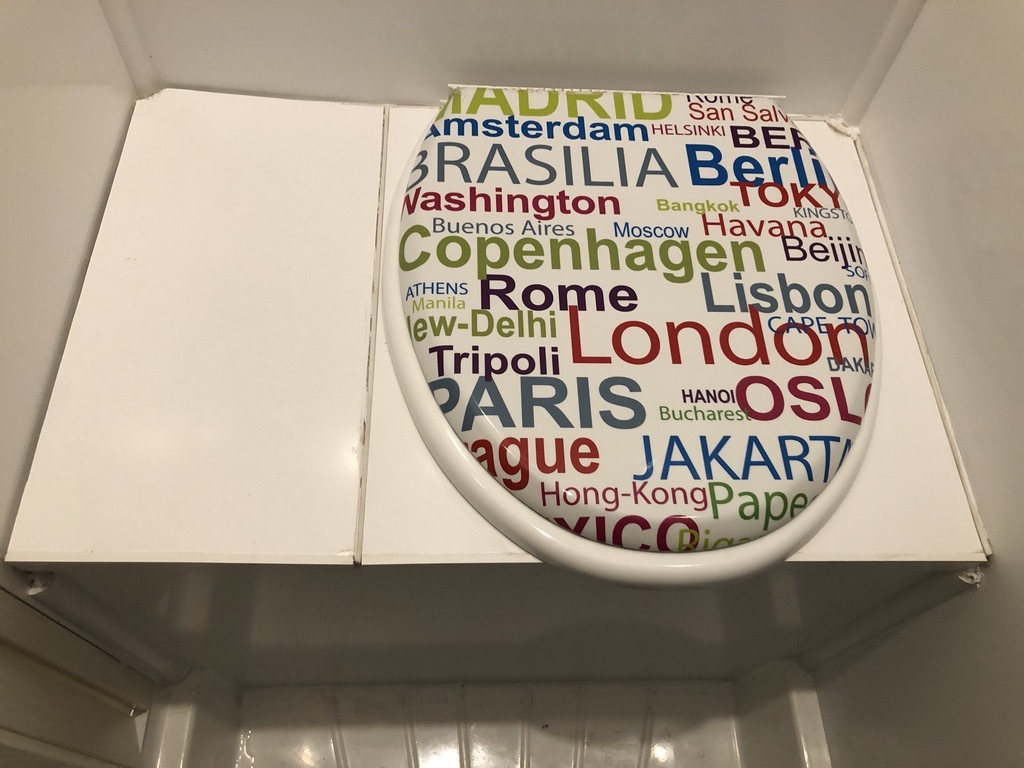
Bedroom
A fixed bed was our number one priority for the van. The size of the bed was dictated by the size of our bicycles which we wanted to store underneath the bed, hence we have a high and wide bed! We fixed six Ikea Skorva brackets and three bed beams to the timber wall battens and added the Ikea Luroy king size slatted bed base (we had to remove a couple of the slats to make it fit).
We both prefer a firm mattress and opted for a supportive reflex foam mattress from Custom Size Beds – the size is 146cm wide x 179cm long x 7cm deep, somewhere in between a double and a king size!
In addition we added a DRY-Mat breathable mattress underlay as a ventilation layer to protect our mattress from damp and mould.
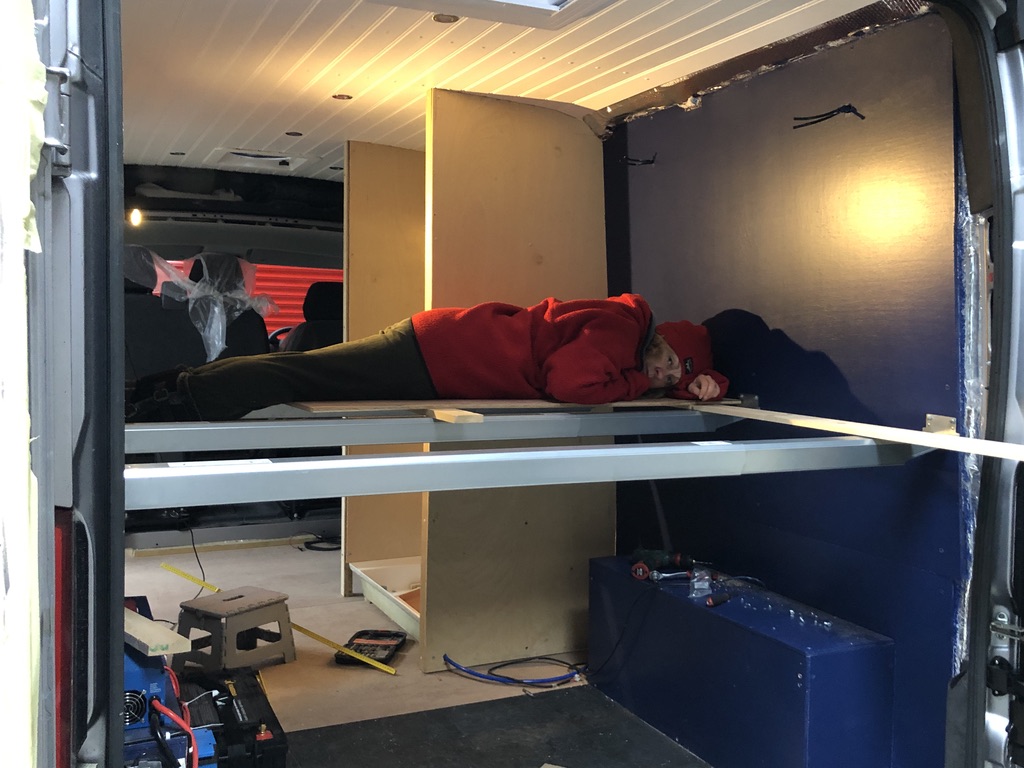
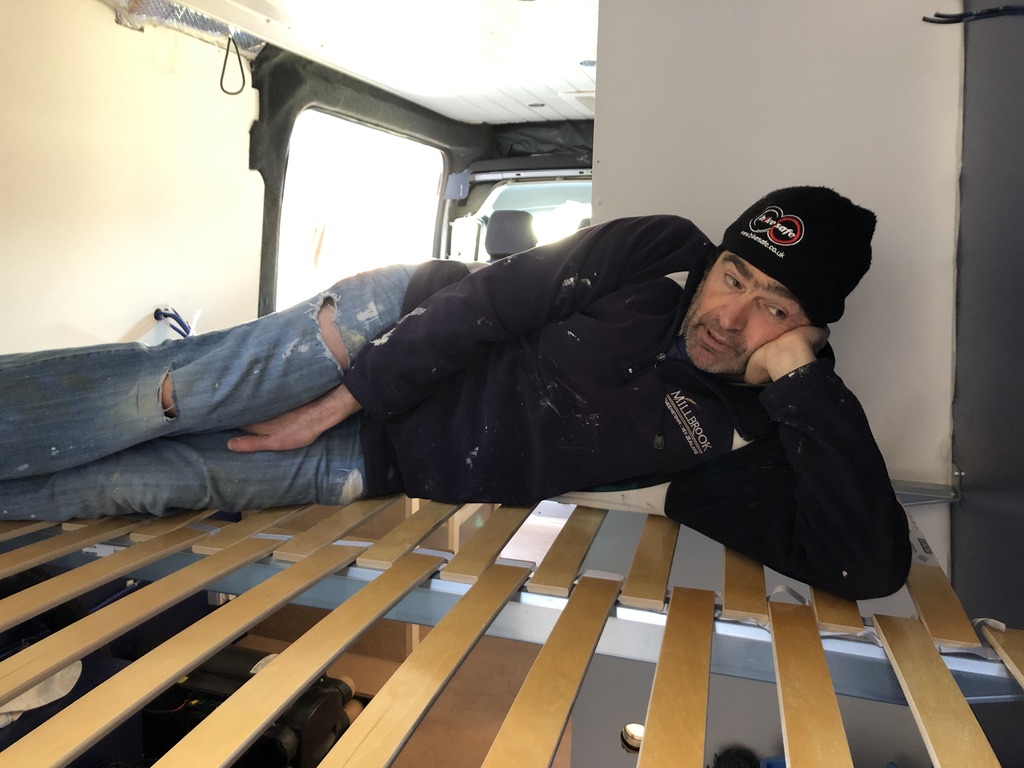
Kitchen
The next stage was building our kitchen framework. The kitchen design was based around our Thetford Triplex oven, a VitriFrigo 60ltr fridge/freezer, and a decent size kitchen sink! We’d seen so many camper vans with sinks you can barely fit a plate in.
We built the framework using 2×1 battens, and used a mix of leftover 6mm & 9mm plywood for the drawers and cupboards, while the cupboard doors we made from the leftover T&G boards.
For the worktops and table we recycled some old oak floor boards by sanding them down and finishing with natural wood oil.
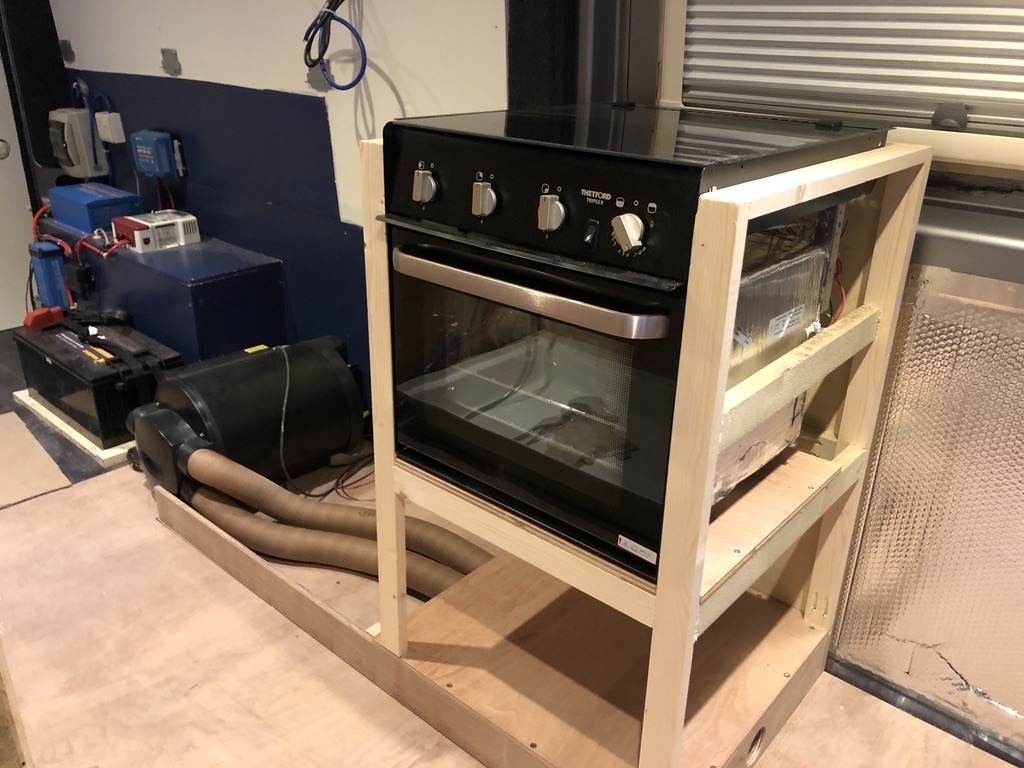
Gas installation
Once we had the kitchen carcass in, it was time to get the gas in.
This was the one job we wanted to have professionally done and certified. We took the van to Leisure Technical Solutions in Lisburn who fitted the 25 litre underslung gas tank we purchased from Autogas 2000. They connected our Thetford Triplex oven and our Truma Combi 4E boiler, and fitted an external gas BBQ point. This stage would have taken us at least a couple of days in awkward spaces with limited tools, but out-sourcing this job meant it was completed safely and professionally in less than 24 hours.
We installed carbon monoxide and smoke alarms as soon as the gas installation was complete, and added a fire extinguisher and a fire blanket.
Storage and seating
Dave designed and built all the overhead storage cupboards with 2×1 frames, and 9mm plywood for the doors. We had just about enough room to squeeze in a bench seat, with storage underneath, in the lounge/dining area. Again this was built with 2×1 frames and fronted with leftover T&G boards. We topped it with a couple of foam cushions recovered and recycled from an old sofa we had.
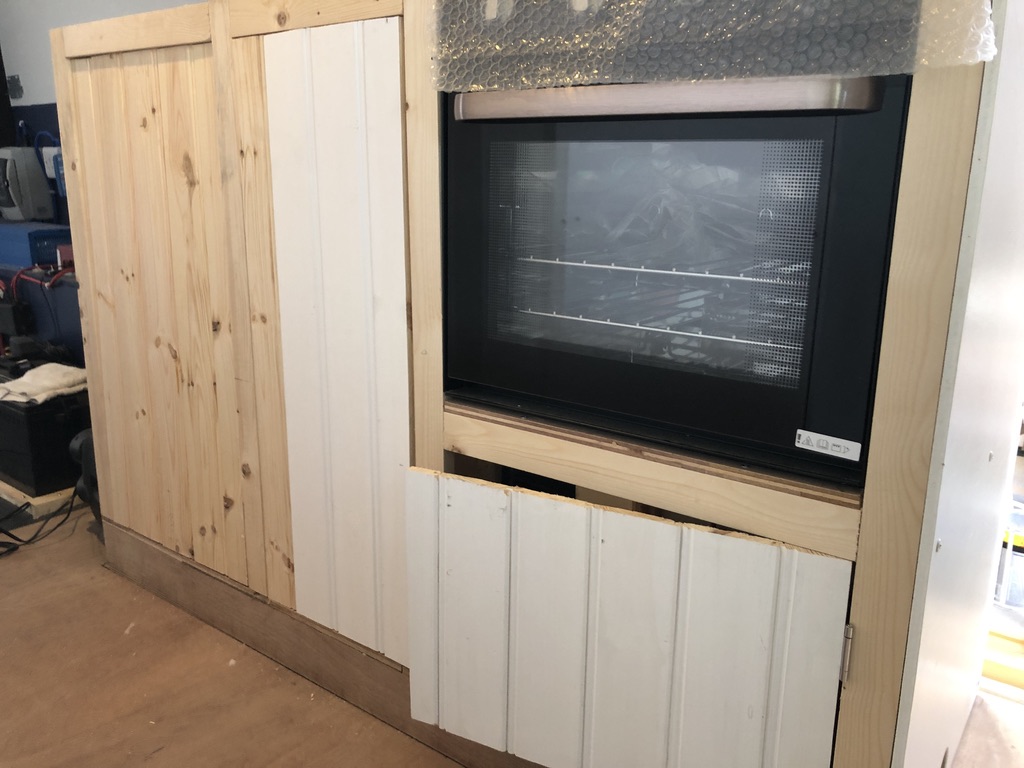
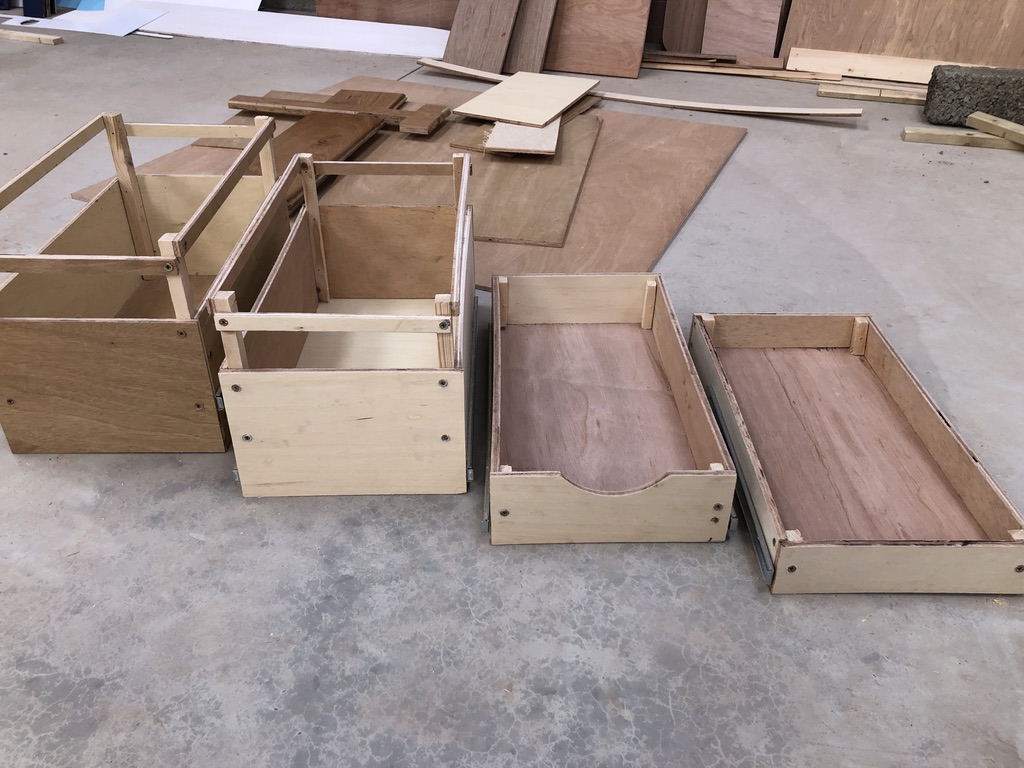
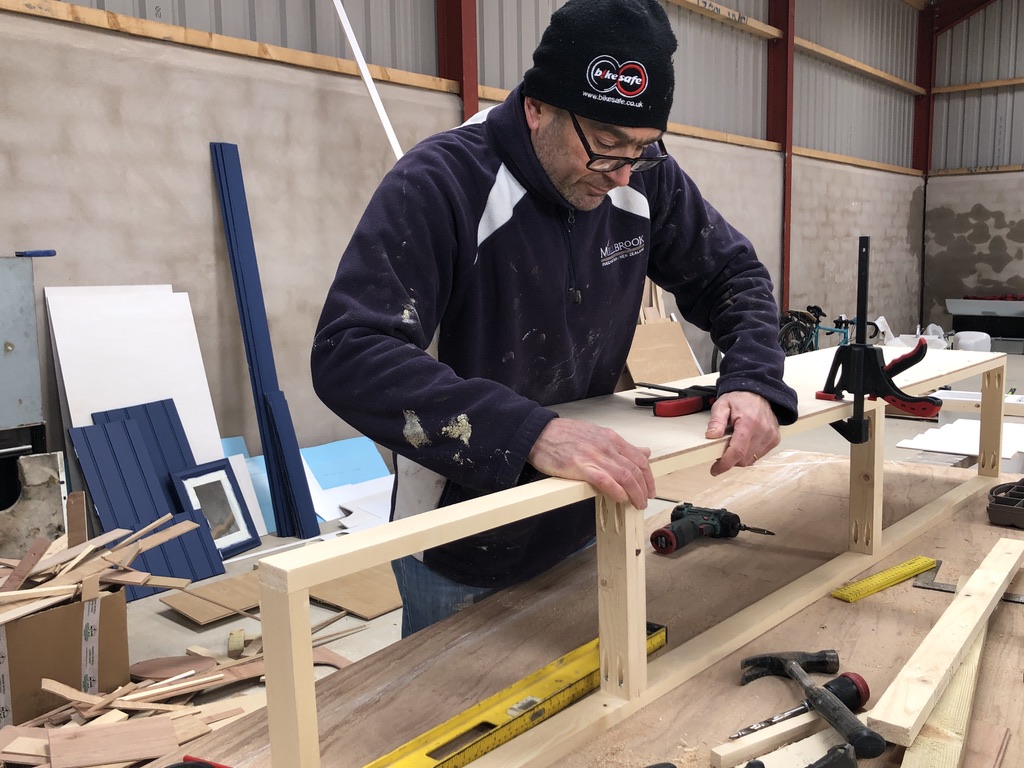
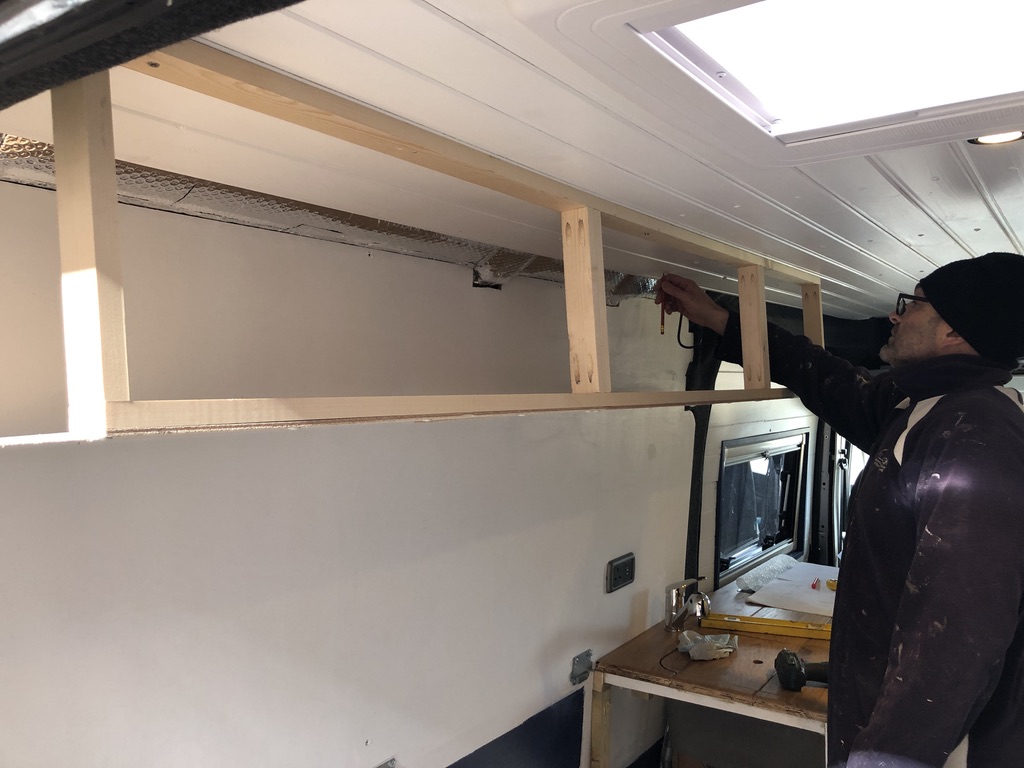
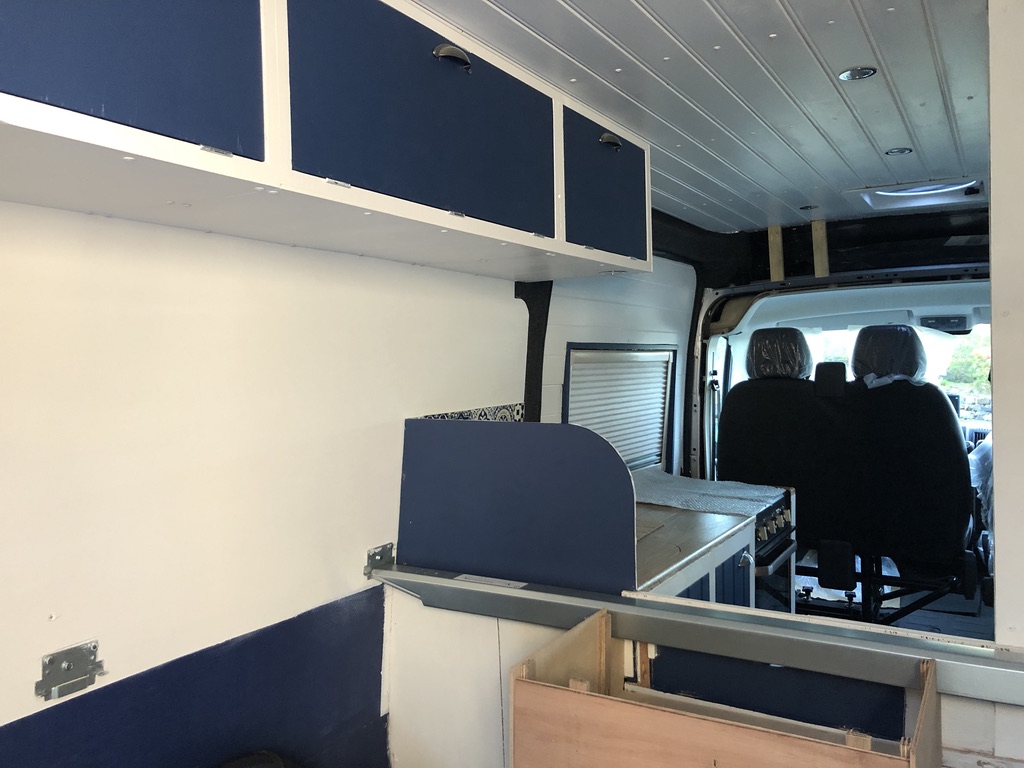
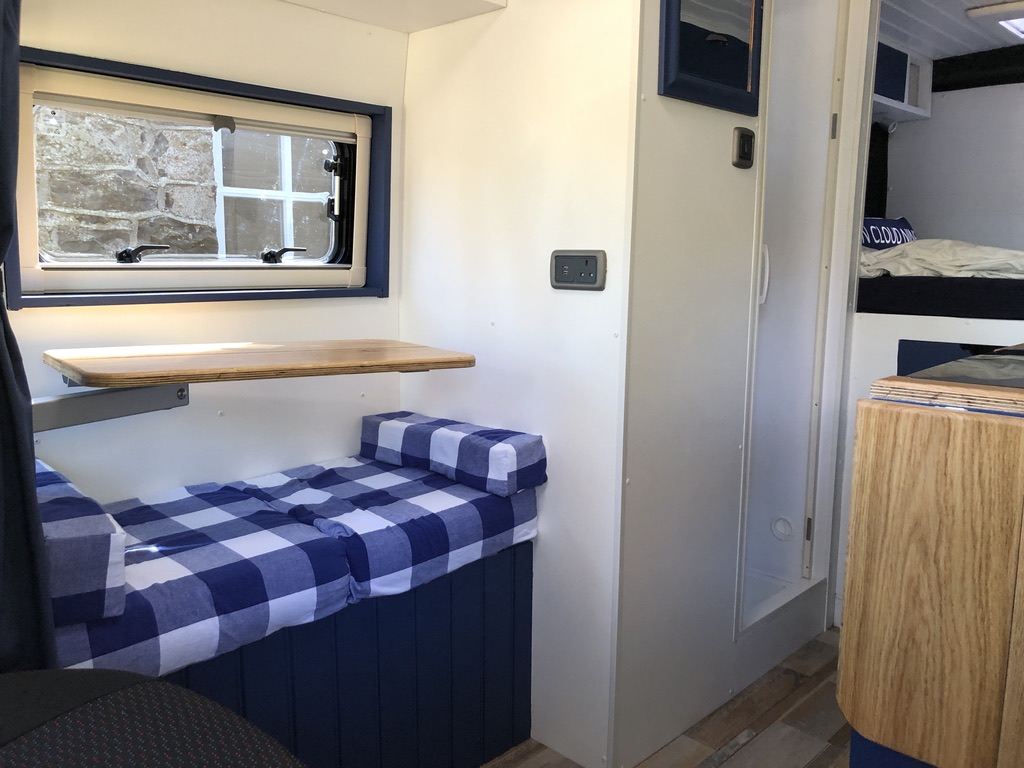
Finishing Touches
There were lots of these to do! In fact there is no such thing as a finished camper van build – it is a constant work in progress!
- Making window frames.
- Panelling the sliding door.
- Connecting the water monitor.
- Plumbing in the kitchen sink and tap.
- Connecting the fridge & filling it!
- Covering the overhead cab with plywood trim (templates which we had custom made broke in transit!).
- Adding stretch carpet trim around the rear and passenger doors.
- Laying self-adhesive vinyl planks as the top floor.
- Tiling the kitchen splash back – we used peel & stick tiles as a lightweight, cheap option.
- Adding handles and magnets to drawers and cupboard doors.
- Top coat painting.
- Adding the slide out tray to the garage with bicycle fork mounts.
- Fitting the Lagun swivel table leg.
- Adding the soft furnishings, hooks and mirrors.
- Adding some funky custom made Cloud Nine decals!
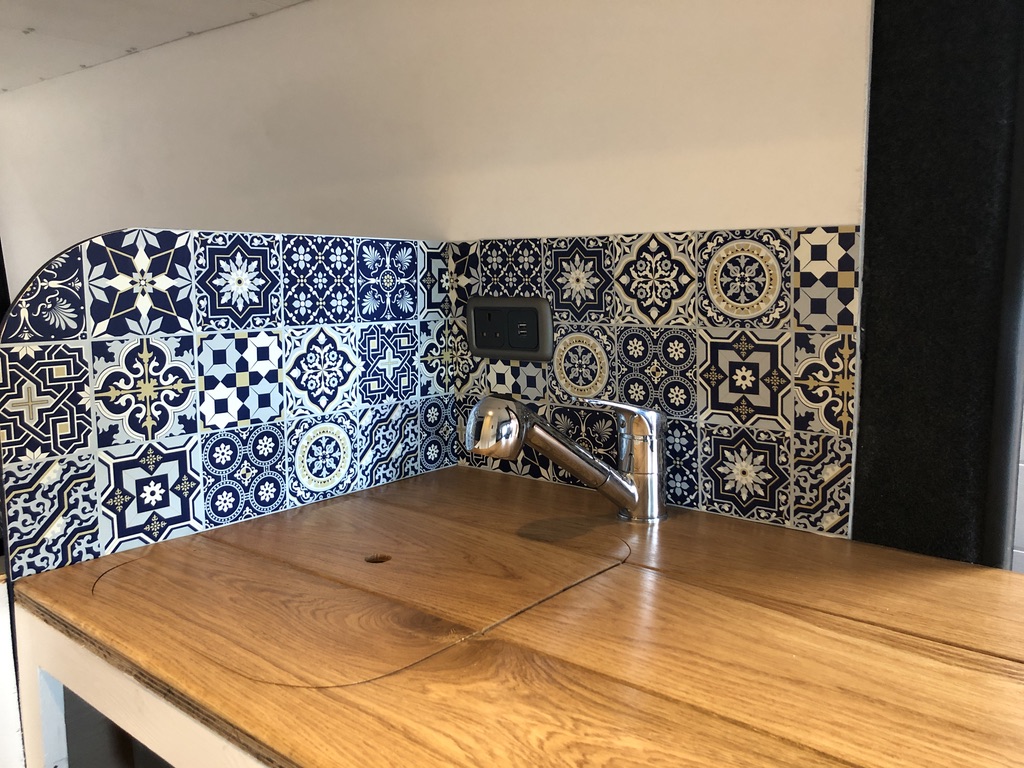
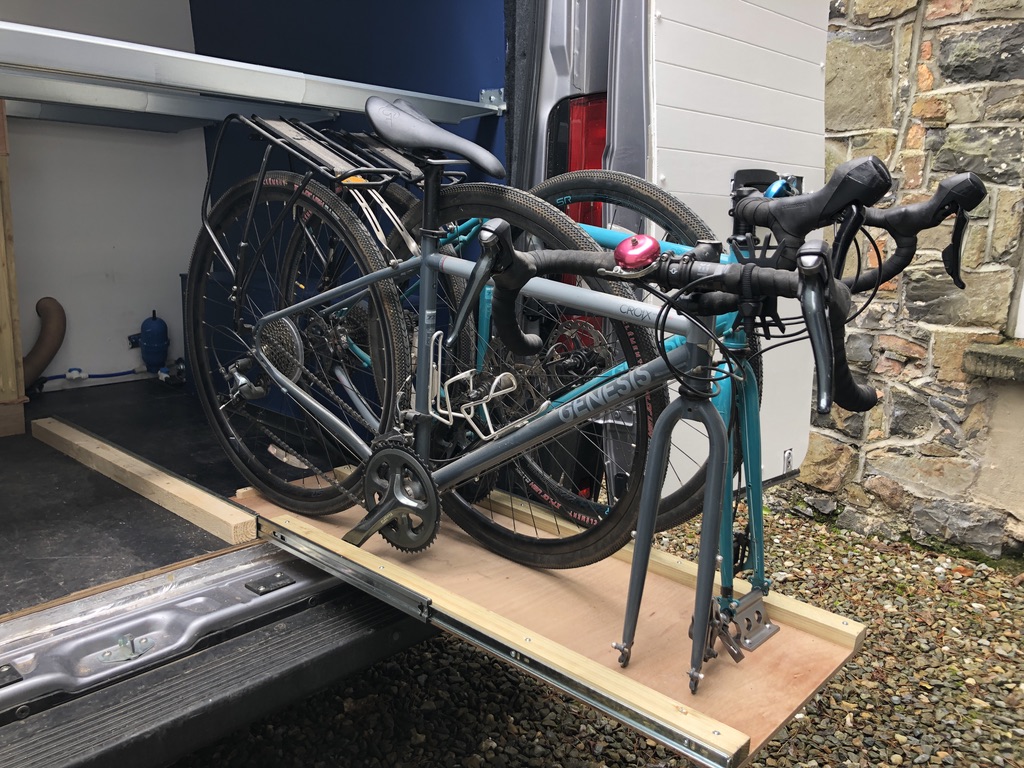
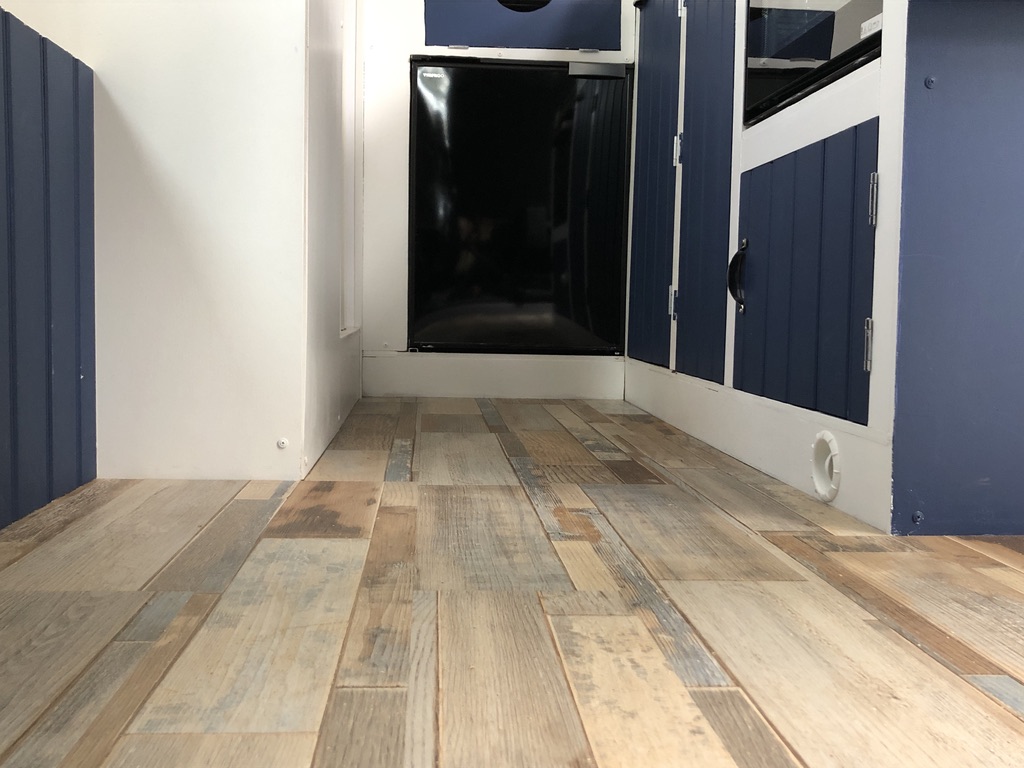
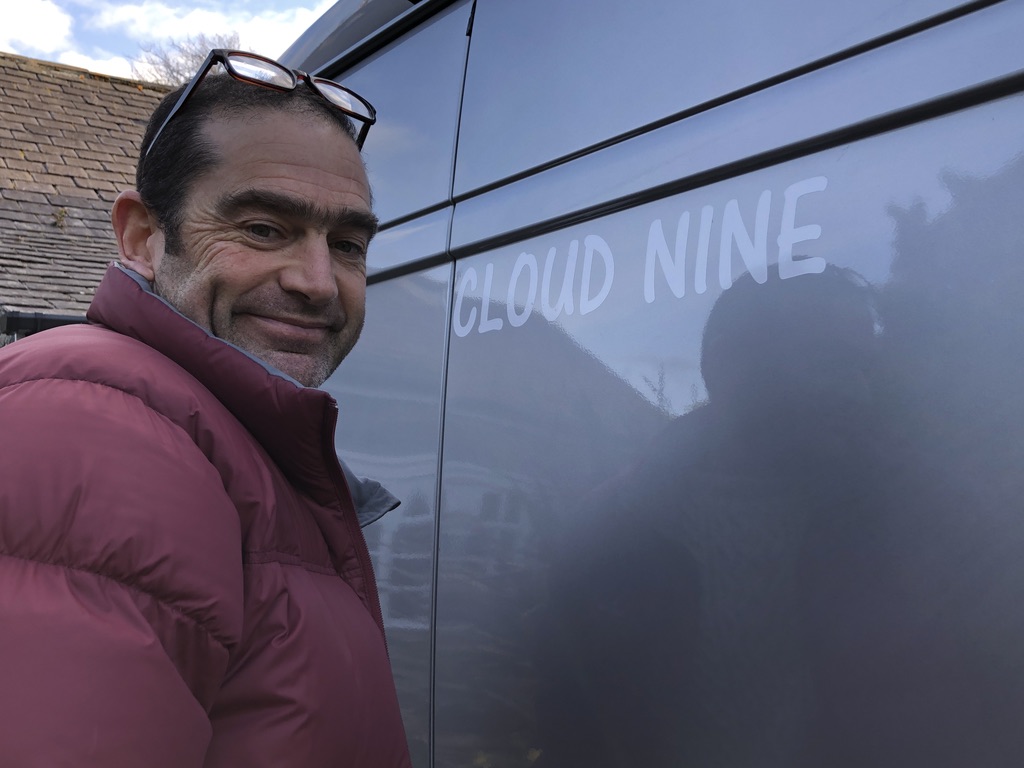
Completion!
After 16 weeks of blood, sweat and tears our van build is practically complete and ready for a trial run. It is full of imperfections, but they are our imperfections, and if anything does go wrong, as it invariably will, we should have a fair idea of how to get to it to fix it!
Building a camper van during a global pandemic and the coldest, darkest months of the year is not something we would recommend, or do again. We started our van build the first week of December 2020 when the days on the North Coast of Ireland are very, very short. There were no electric lights in the shed so we relied solely on natural daylight from the roof skylights. Nor was there any source of heating to speed up the setting process of sealants and adhesives, or the drying of paint. In fact for the first few weeks of our build process we were contending with below freezing temperatures on a daily basis!
What we didn’t add to the process of building a camper van was that at every single stage we spent countless hours either standing in it and just looking at it, or hours lying underneath it trying to work out where everything was going to go!
We learned a lot during the entire process and are very proud of what we accomplished together. We couldn’t have done it without all the fantastic resources we found online, in particular the YouTube videos by Greg Virgoe, The Restoration Couple, VanLife Conversions and CamperVibe.
We will be forever thankful for all the inspiration, advice and motivational support we received from so many great online van build communities. How people ever built their own camper vans before the internet is beyond us!!!
If you read this far, well done! If you want to know any more details on how we built our camper van pop a question in the comments below or drop us a line hello@schindlersontour.com
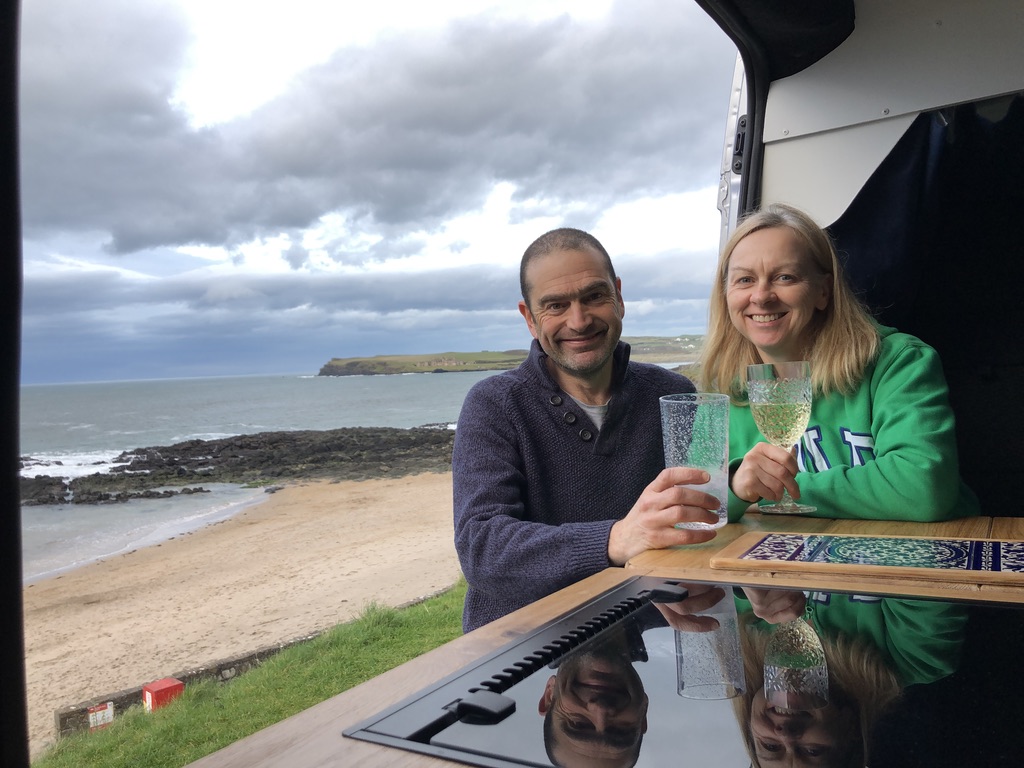
Disclosure – We are participants in the Amazon Associates Program and as Amazon Associates we earn from qualifying purchases. There are affiliate links in this post which means we may earn a small commission/referral fee if you purchase the product we recommend by clicking on the link. There is no extra cost to you, and be assured that we ONLY ever recommend products that we truly believe in and have tried and tested ourselves. If you use our links, we thank you!